Bernd Fleschenberg (COO TSR Recycling GmbH & Co. KG) and Christian Blackert (COO TSR Automotive GmbH) were joined by the Minister for Economic Affairs and Energy of the State of North Rhine Westphalia (NRW), Mona Neubaur, Norbert Rethmann (Honorary Chairman of the Supervisory Board of RETHMANN SE & Co. KG), Dr Arnd Köfler (CTO thyssenkrupp Steel Europe AG) and Jens Rubi (Head of Circular Economy Mercedes-Benz AG) to celebrate the official opening of TSR’s new processing plant at its branch in Duisburg.
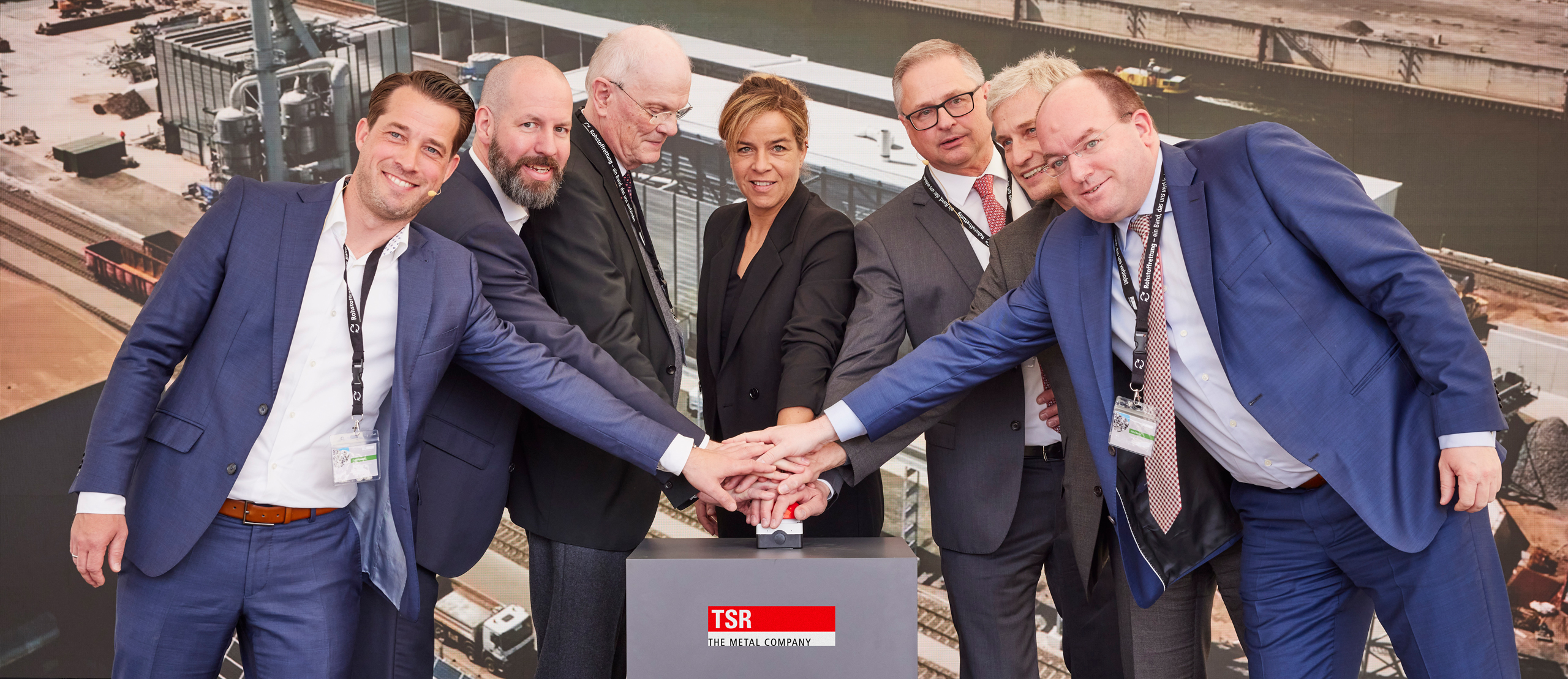
Completed in just 12 months, this new facility will now be able to process up to 450,000 tonnes of input material (such as end-of-life vehicles, mixed scrap and large household appliances) every year and transform it into the recycled product TSR40. Thanks to the newly developed measuring, detection and separation technologies at the plant, the company is able to identify and remove elements in the raw material that may disrupt production processes as well as to determine the precise levels of any accompanying elements (e.g. copper, nickel and chromium). The decision was made to build the new facility after TSR Recycling developed an innovative system to produce TSR40 – a certified, high-quality recycled product that reduces CO2 emissions and cuts consumption of virgin raw materials and energy when used to manufacture steel.
The company will continue to further develop the process together with its project partners VDEh-Betriebsforschungsinstitut GmbH, Hüttenwerke Krupp Mannesmann GmbH and thyssenkrupp Steel as part of the publicly sponsored REDERS research project (REDERS is a German acronym for ‘reducing CO2 emissions by increasing the rate of recycled materials in steel production’).
Thanks to TSR40, TSR Recycling is now able to supply the steel industry with a raw material that is not only energy, climate and resource-friendly but also enables the volumes of recycled material used in steel production to be significantly increased without there being a loss in quality. The new processing plant in Duisburg is, therefore, not just an important milestone for the whole of the industry. It is also a flagship project that will enable the steel industry and other steel-processing sectors – such as the automobile industry – to transform their systems and manufacture greater volumes of sustainable high quality products.
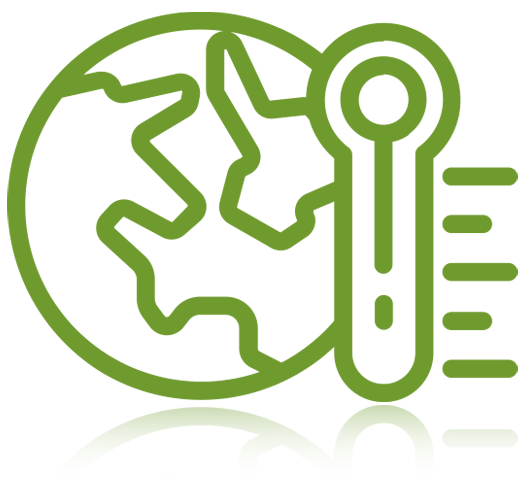
“We will only be able to have a net zero industry, easy access to raw materials and sustainable business practices if we make the very most of the potential of the circular economy.”
Mona Neubaur, NRW Minister for Economic Affairs and Energy
NRW Minister for Economic Affairs and Energy, Mona Neubaur, believes both the project and the new facility to be pioneering investments. She praised them, saying: “We will only be able to have a net zero industry, easy access to raw materials and sustainable business practices if we make the very most of the potential of the circular economy. Innovative projects that enable closed loop systems to be set up make a significant contribution towards both conserving raw materials and energy and reducing greenhouse gas emissions – and this is particularly true when such projects involve energy-intensive sectors. The steel scrap processing plant here in Duisburg, which was developed by a group of local companies, very much underlines this fact. The circular economy needs such industrial partnerships along the whole of the supply chain so that ambitious, game-changing projects can be successfully implemented.”
Dr Arnd Köfler, CTO at thyssenkrupp Steel, explained: “Decarbonising steel production is going to be a massive task. We reached an important milestone when we commissioned the construction of our first hydrogen-run direct reduction facility. We won’t be waiting until our plant has been completely transformed, though. We intend to use every avenue that is open to us today to reduce our plant’s CO2 emissions. Thanks to TSR40 and the high quality systems used to process scrap steel, we have now been given the opportunity, for the very first time, to use a top quality, certified product in our furnaces as well. This will further help us to reduce our CO2 emissions – something that will also benefit our customers.”
Jens Rubi, Head of Circular Economy at Mercedes-Benz AG, explained how car manufacturers viewed the situation: “The materials used in our Mercedes-Benz vehicles must meet the highest standards. Our company is researching new, resource-friendly materials to unite sustainability and luxury. We believe the circular economy will play an important role here. If we are to reach our next milestone – our #ambition2039 – then we must stick to our motto ‘every action counts’.”
“High quality recycling is an important element to reducing our dependency on virgin raw materials – especially in these times of disrupted supply chains,” commented TSR Managing Director, Bernd Fleschenberg. “Our recycled product TSR40 illustrates, therefore, how raw materials can be sustainably secured in Germany and Europe and will enable us to cover a considerable amount of the industry’s future demand for raw materials. Besides the positive impact it will have on protecting the environment and curbing climate change, this development is also our contribution towards a sustainable circularity strategy and achieving the goals of the European Green Deal.”
Image credits: © TSR