Many experts believe that the recovery and reuse of waste heat is one of the ‘slumbering’ giants of the energy transition. A few years ago, researchers calculated that the amount of unused waste heat produced by German industry was enough to heat six million 2-person households in Germany. In Bad Säckingen, a town situated in the Baden region, REMONDIS’ joint venture business Alunova Recycling is carrying out tests together with the Swiss energy provider Energiedienst to see how the waste heat generated during the pyrolysis of aluminium waste can best be used. And they are entering unchartered territory as there are no other comparable facilities to be found here in Germany.

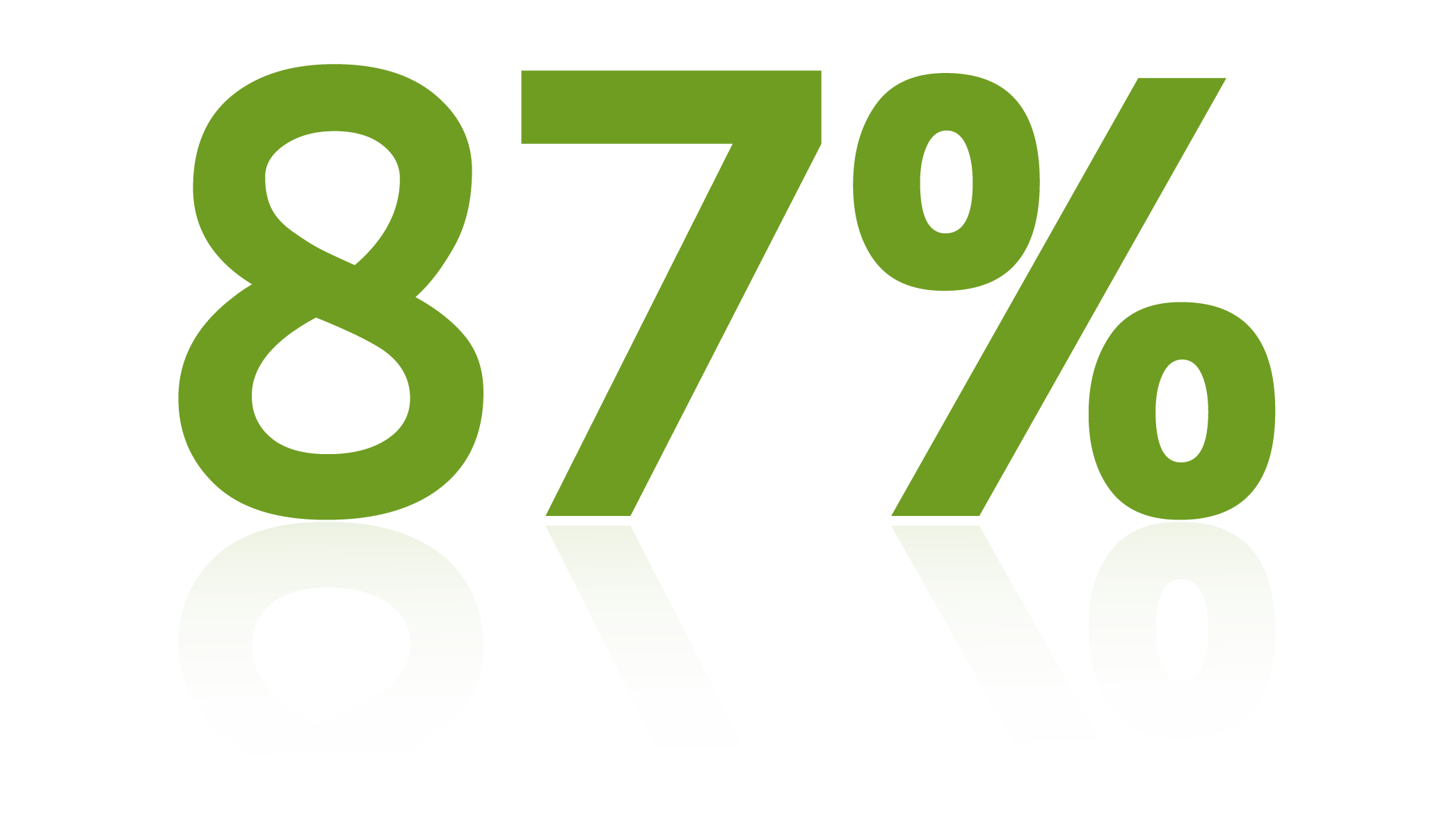
Aluminium is already one of the most recycled raw materials in Germany with a recycling rate of 87%.
For a long while now, the focus of companies in Germany has been on energy-saving measures as these are quick and easy to implement. Things are beginning to change now though because it will be extremely difficult for businesses – especially those operating in energy-intensive industries – to achieve the ambitious carbon-reduction and energy-saving targets without making the most of their waste heat. Besides feeding waste heat into local district heat networks, manufacturing firms can also use it to heat their own buildings, to generate electricity via a turbine or to return it to production processes. As to which waste heat recovery system is right for a business and how best it can be used depend on a number of factors such as the production process, the production energy and the location.
In this particular case, Alunova recycles composite packaging containing aluminium that has been collected in recycling sacks and bins or that has been generated as part of packaging material production processes. Aluminium is already one of the most recycled raw materials in Germany with a recycling rate of 87%. And, looking at its energy footprint, it certainly makes sense to recycle aluminium: this process requires less than one-tenth of the energy needed to produce aluminium from virgin raw materials. Together with its workforce of 43 employees, Alunova produces around 11,000 tonnes of recycled aluminium for a variety of uses every year.
Making the most of the pyrolysis gas
The production process is simple: the bales of composite materials containing aluminium (which are supplied by the sorting plants run by the Dual Systems, Germany’s sales packaging collection scheme) are separated, contaminants and iron are removed and the remaining materials transferred into an incinerator. All of the substances apart from the aluminium are incinerated at a temperature of around 700°C. External energy is not needed for this process as all of the energy required to heat up the contents is provided by the substances adhering to the composite materials. All in all, though, Alunova consumes 7,500 MWh of energy every year for its treatment processes, in particular for its shredding facilities, ventilation system, oxidizing roasting unit, conveyor technology and flue gas cleaning system.
The main product generated by this recycling system is a variety of different-sized aluminium pieces. The larger pieces are used by aluminium smelting firms to produce aluminium or are sent to steelworks where it is used as an auxiliary material in the smelting process. The smaller pellets are primarily used as an auxiliary material at foundries to produce iron alloys.
The pyrolysis process also generates, among other things, energy-rich pyrolysis gas. Up to now, this gas has been burned to destroy any pollutants and then cooled down with water. It has then been cleaned with additives, filtered and finally released into the atmosphere via the chimney. This cooling process consumes a large amount of energy and the heat escapes into the environment via the chimney.
Alunova managing director Georg Möller commented: “If this project turns out to be a success then Alunova will have taken a huge step forward as regards the EU’s reduction target of 55% by 2030.” However, the high ash content and the chlorine in the flue gas are problematic for any technical facility – the ash because it can lead to wear and tear and deposits building up and the chlorine because it is highly corrosive. The high levels of moisture in the gas mixture are also a real challenge.
“If this project turns out to be a success then Alunova will have taken a huge step forward as regards the EU’s reduction target of 55% by 2030.”
Georg Möller, Alunova Managing Director
The test facility
Alunova and Energiedienst are currently in the advanced experimental phase. A test facility was built on Alunova’s grounds in 2022 and cost 250,000 euros. The facility also received an 80,000-euro grant from the German state of Baden-Württemberg via the Karlsruhe Institute of Technology (KIT). Research work is being carried out at the facility to find out what the conditions in a recuperator deployed for recovering heat must be so that electricity and/or district heat can be generated without the pipes and machines suffering wear and tear, clogging up or being chemically corroded. The results so far have not been completely satisfactory. “But we’re on the right path,” Möller confirmed. The tests are due to have been completed by the summer and then a decision will be made, based on a business case, whether a large-scale facility can be built or not.
At the end of the day, there is great potential here: Alunova could use its pyrolysis gas to generate enough electricity so that 50% could be used for its own site and 50% fed into the national grid. At the same time, heat could be produced to supply the base load for the nearby district heat network that would be sufficient for 10,000 flats.
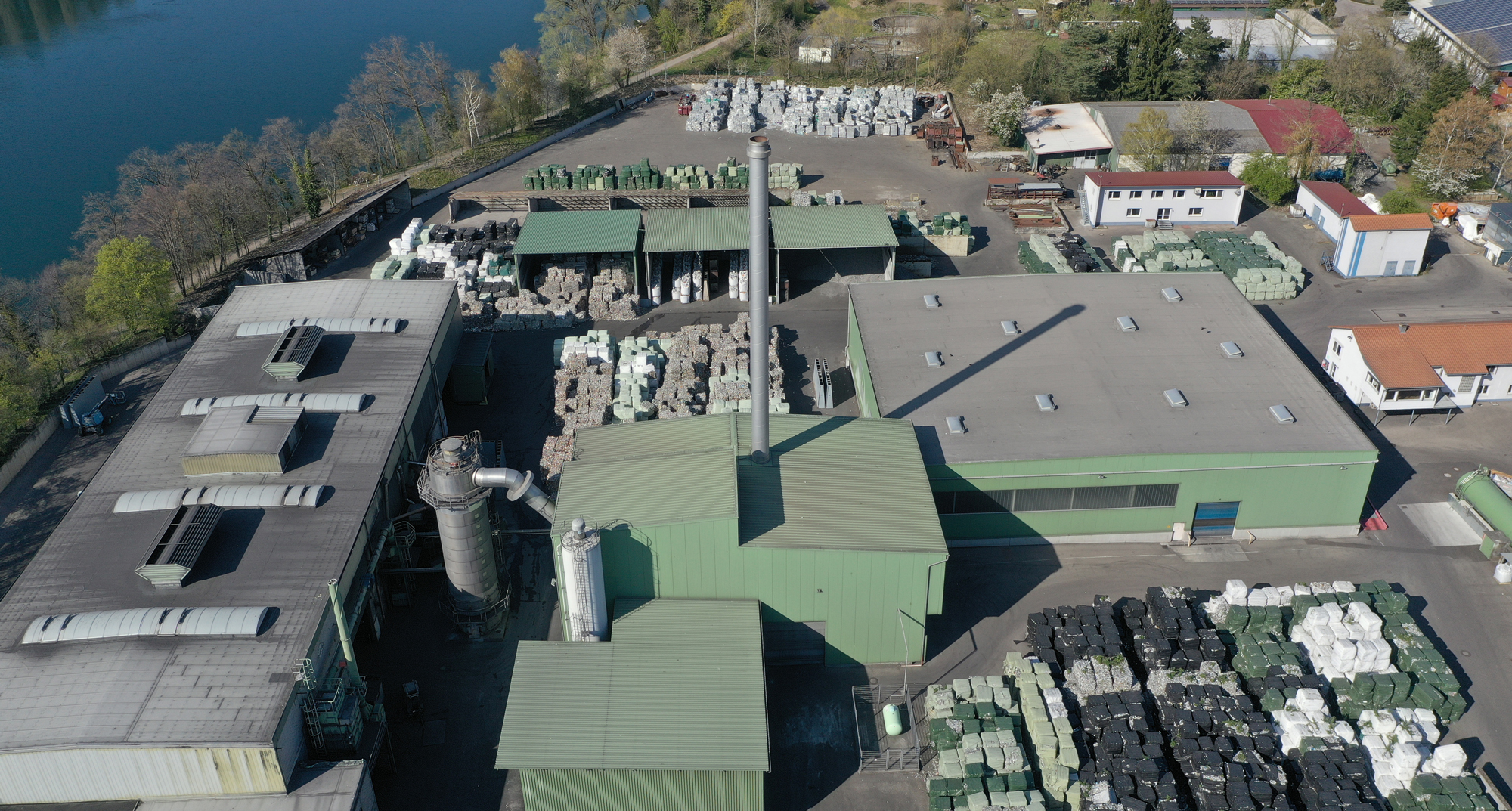
Image credits: © Alunova