Mandatory recycling rates increased
The new Packaging Law, which has been in force since 01 January 2019, sets out a number of recycling targets until 2022 to ensure an ever increasing volume of plastic packaging is recycled. One of the most important targets here is that materials recycling should increase from the current rate of 36% to 58.5% in the first year and to 63% from 2022 onwards. Plans are, once the last recycling rate has been reached in 2022, to review the recycling targets within the following three years and push them up even further if necessary. More money needs to be invested in state-of-the-art sorting technology if such ambitious recycling rates are to be achieved. Once again, REMONDIS is showing how this can be done having opened up a new high performance sorting facility in Erftstadt near Cologne, which was commissioned at the same time the new Packaging Law came into force.
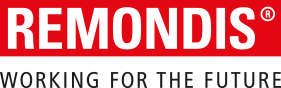
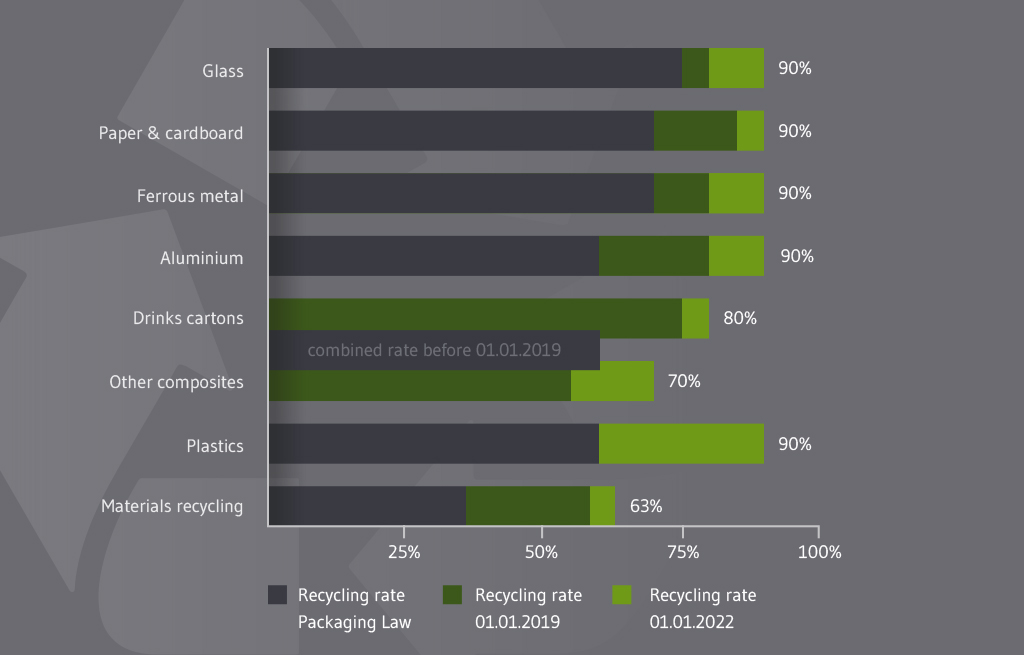
A capacity of 150,000 tonnes a year
All in all, Germany has a relatively high volume of municipal waste – around 40 million tonnes are produced every year – which means that the country’s sorting and recycling plants do not need to worry about whether they have enough material or not. The challenge that these businesses do have to face, however, is how to improve the range and quality of the materials that can be recovered for recycling. And this challenge must be dealt with if these new and ambitious materials recycling rates are to be met. Which was precisely why, during the planning phase, REMONDIS not only put thought into how big the sorting facility in Erftstadt should be but also into how many types of materials could be recovered and separated from each other.
The range of the recovered materials must be improved, if the new recycling rates are to be met.
Handling a throughput of up to 150,000 tonnes a year (120,000 tonnes of which is lightweight packaging from the recycling bins), the new plant is one of the biggest of its kind on the German recycling market. There was also nothing accidental about the choice of the location either. Built on a large site in an industrial area near Erftstadt, the facility has no immediate neighbours who could be disturbed by its operations and is very close to the City of Cologne and the densely populated Rhineland region.
The challenge is how to improve the range and quality of the materials that can be recovered for recycling. This is the only way to achieve the ambitious goal of growing materials recycling rates.
State-of-the-art sorting & screening technology
The packaging material is transformed into raw materials in the facility’s three buildings. Each building has its own specific role, either accepting the incoming material, sorting it or storing it. The hall responsible for handling the incoming material is equipped with a gantry crane, which is easily able to deal with the large volumes delivered each day. The recycling bags are automatically opened so that the material can be transported along a conveyor belt that is, all in all, around 1.5 kilometres in length. This enables the material to undergo many different sorting and screening stages helping to ensure that as many different types of plastics can be recovered and separated from each other. Various kinds of equipment are used here including three vibrating screens, a drum screen, a total of 21 near infrared separators, four air classifiers and two ballistic separators. With the quality of the recovered materials being so high, they can be sold on to manufacturers as environmentally and climate friendly recycled raw materials – helping to significantly reduce the demand for so-called primary raw materials, which have a considerably greater impact on the environment. At the end of the day, one tonne of recycled plastic saves 1.2 tonnes of CO2 compared to virgin plastic produced from crude oil.
Even glass is recovered for reuse
The plant in Erftstadt is able to recover and separate a large number of different materials so they can be reused. These include polyethylene (PE), polypropylene (PP), polystyrene (PS), PET bottles, PET trays, drinks cartons, tinplate, aluminium, plastic film, paper and cardboard and even glass. The latter is one of the special features of the Erftstadt facility.
Every tonne of recyclable material that is recovered for reuse helps conserve our planet’s resources and protect the environment.
Any residual materials left over after the sorting process are put through a further screening system, which is when the outthrow material glass is recovered. Looking at the results of the test operations, the facility is expecting to recover around 2,000 tonnes of glass a year – a figure that no other materials recovery facility is able to match. Just a very small amount of the input material ends up being sent, for example, to the cement industry as refuse-derived fuel (RDF) for producing electricity and heat. For the most part, this RDF is made up of mixed plastics and sorting residue which has been classified by the facility as being non-recyclable.
A wide range of materials recycled
The different kinds of sorted plastics that have been recycled for reuse are sold on to the plastics processing industry in Germany and other European countries. Any ferrous metals and aluminium are sent straight to steelworks and aluminium processors via REMONDIS’ subsidiary, TSR, and other metal processors. Any paper and drinks cartons are processed at different paper mills. Materials that are to be used to produce energy are transformed into RDF at the company’s own plants and then used in its own power stations or sold on to the cement industry. Thanks to its work, REMONDIS’ sorting plant in Erftstadt should help to close more material life cycles and fulfil the regulations set out in the new Packaging Law.
Image credits: © REMONDIS