Bad news for the construction sector
Gypsum. Finding ways to recycle this white mineral so that it can be reused will play an ever more important role in the future, as Germany moves away from producing energy from coal and gradually closes down its coal-fired power stations – the recycling sector’s most important source of gypsum. Bad news for the construction sector as gypsum can be found in wall plaster, screed and roof tiles as well as in stud walls made with gypsum plasterboard. More than 230 square kilometres of plasterboard are produced in Germany every year. All in all, the annual demand for calcium sulphate raw materials lies at around 9.5 million tonnes, in particular from the plaster and cement industries.
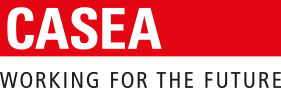
Hardly any gypsum is being recycled at the moment
There will be a huge gap in the market once the gypsum from flue gas desulphurisation systems – known as FGD gypsum – can no longer by supplied as a by-product of the chemical process at power stations. In 2010, more than half of all gypsum requirements was covered by FGD gypsum; this figure is expected to have fallen to just 30% by 2030. At the same time, the volume of waste plasterboard is steadily growing.
In 2030, just 30% of gypsum requirements will, in all likelihood, be covered by FGD gypsum.
According to a study published by the UBA [Federal Environment Agency], around 280,000 tonnes of this material were discarded in Germany in 2015. Experts believe this figure will have increased to up to 670,000 tonnes by 2030. The situation is being aggravated by the fact that only a fraction of these discarded gypsum-based products are actually being recycled – around seven percent in 2015. Landfill space for this material is also getting scarce. Over the short to medium term, there will be bottlenecks at landfills for category 0 and I substances and there will be less space at mines for depositing this material. The situation can only get worse.
Both a blessing and a curse
REMONDIS believes that these growing volumes of waste plasterboard could present a great opportunity as it gradually becomes more and more difficult to obtain gypsum. Leading manufacturers of gypsum-based products, including REMONDIS’ sister company CASEA GmbH (experts for both natural and FGD gypsum), are looking at alternative ways to get hold of supplies once FGD gypsum is no longer available to the market. One solution is to extend or reopen old quarries so that more natural gypsum can be mined. In Germany, the majority of this resource can be found in the Harz region, in the so-called gypsum karst belt. Mining natural gypsum, however, is still impacting on the environment. One of REMONDIS’ principles is to find and implement solutions that help curb global warming and conserve natural resources. The UBA is also calling for concrete measures that will provide an environmentally friendly solution to this problem.
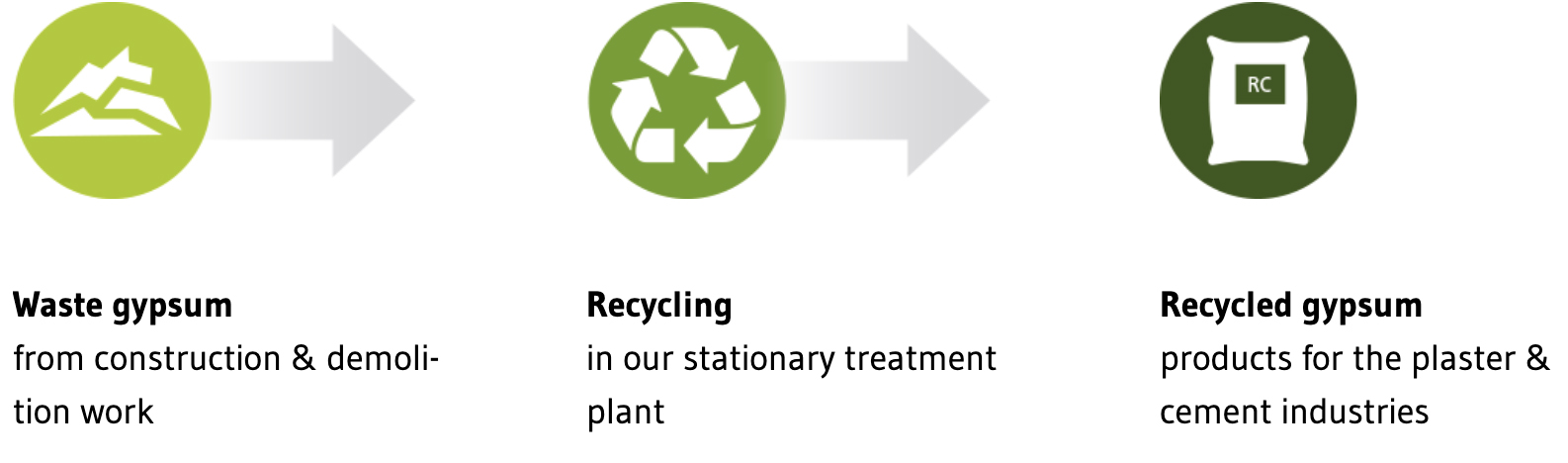
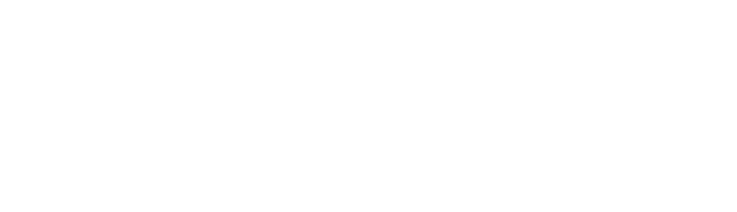
of pure gypsum are produced at the plant in Zweibrücken every year which can then be directly reused by industrial businesses.
The goal must be to recycle & reuse gypsum
The declared goal here is to gradually increase the amount of recycled gypsum used in production chains – both to preserve natural resources and to push forward recycling in this area so that the gypsum can be reused. Reuse is the best form of recycling and this is not a problem for gypsum as our recycling process does not change the raw material in any way whatsoever.
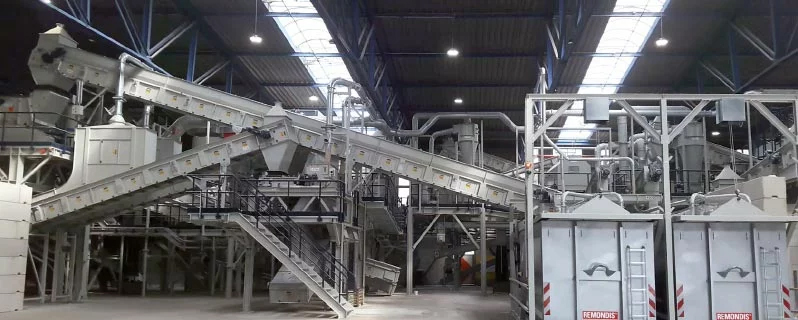
The plant in Zweibrücken was just right for setting up a gypsum recycling facility
The benefits of recycling gypsum-based plaster
REMONDIS itself offers a sustainable and environmentally friendly solution: every year, its business in Zweibrücken transforms plasterboard and moulded plaster into up to 72,000 tonnes of pure gypsum that can be directly reused by industrial businesses. The facility, which had previously been home to a waste sorting plant until 2009, is one of just four across the whole of Germany – one reason why it is not possible to make the most of the waste plasterboard generated each year. The advantages of this process are obvious. Natural gypsum supplies can be conserved and carbon emissions are also reduced. Free landfill space can be used for materials that really cannot be recycled for reuse. The system that REMONDIS uses makes the very most of the gypsum as the gypsum retains its physical and chemical properties so that it can be recycled endlessly.
Efficiently using residual materials
The facility is run by REMONDIS GmbH & Co. KG, Region Südwest [South-West division], which had been issued a permit to build a production plant back in March 2017. It is currently being trialled and will, in the future, be able to process plasterboard from a large catchment area. Once the incoming material has been pre-sorted, it is processed into high quality recycled gypsum in a number of steps. The final product, which has official end-of-waste status, stands out thanks to its high level of purity, its low moisture content and the fact that its grain size can be adjusted to meet specific customer requirements. The recycled gypsum can be used by the plaster and cement industries for a whole variety of applications and can be used straight away – further processing is not necessary. Besides recovering the gypsum, the paper can also be extracted from the plasterboard and recycled for reuse in the paper industry. By doing so, REMONDIS has succeeded in closing two different material life cycles.
Top quality recycling will be taking place in Zweibrücken in the future.
REMONDIS has built a facility in Zweibrücken that unites the components of different plant suppliers to create a new concept. The state-of-the-art technology ensures that the stringent quality standards set by the Bundesverband der Gipsindustrie [German Gypsum Association] are met at all times.
Image credits: image 1, 2: © REMONDIS; image 3: Adobe Stock: honeypicture