25,000 tonnes of organic waste a year
It is becoming an ever greater challenge for large German cities to coordinate, transport and sustainably recycle their volumes of waste. This is also true for Frankfurt am Main where the approx. 400,000 households discard 25,000 tonnes of organic waste into their organic bins every year. This major city – an international finance and exhibition centre that has to cope with roads clogged with traffic and the highest number of commuters in Germany – sees this recycling opportunity as a way to improve their environmental footprint.
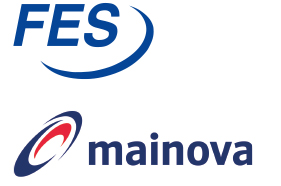
Perfecting the recycling chain
Which was why an anaerobic digester was built in Frankfurt’s Eastern Harbour district (just a few kilometres from the city centre) to treat organic waste back in the 90s. Since then, the facility has been run by FES’ subsidiary, RMB Rhein-Main Biokompost GmbH. FES is a joint venture between the City of Frankfurt (51%) and REMONDIS (49%).
Orange peel, coffee filters and leftover food mixed with garden waste and leaves. This is the mixture of materials that FES’ refuse collection lorries take to the organic waste treatment facility.
The recycling chain for this material stream has now been perfected: not only has the capacity of the digester plant been extended so that it can now process 60,000 tonnes a year, the Frankfurt-based energy supplier, Mainova, has also built a biogas processing facility on the site. Since the beginning of 2018, the raw biogas generated from processing the organic waste has been transformed into pure biogas, which is being fed into the gas network and supplied to the households. What’s more, Frankfurt now has one of the most modern digesters for organic waste in Europe.
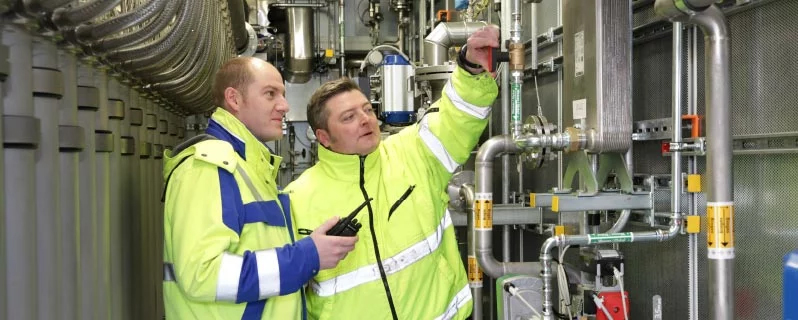
The complex process of producing biogas
Orange peel, coffee filters and leftover food mixed with garden waste and leaves. This is the mixture of materials that FES’ refuse collection lorries take to the organic waste treatment facility. This strong-smelling mixture is a source of renewable energy – a source that is unlikely to ever dry up. At the end of the process, this material has been transformed into high-quality, climate-neutral biogas. The heterogeneous biomass, however, has to go through a number of complex stages before this can happen. First it is cut up in the shredder. The conveyor belts then transport the material to a large mixing tank in which huge rollers blend the waste. Following this, water is added to create a thick mass made up of 70% water and 30% dry matter. “We never use fresh water, though – only process water that we keep in the system by catching and condensing it,” explained Peter Dumin, plant manager at RMB.
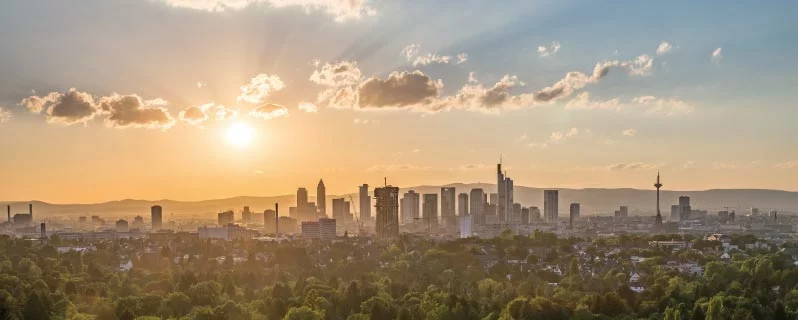
Digestion process helped along by bacteria
Once these different stages have been completed, the feedstock is then pumped into two digesters. The digestion process is activated with the help of special bacteria which multiply rapidly at a temperature of 60°C. The raw biogas generated from this process, however, does not yet fulfil the quality required for the gas supply network. And this is where Mainova’s treatment plant comes into play. It uses a multi-stage procedure to clean and process the raw biogas and turn it into bio natural gas. The facility, which is currently being tested, can transform almost 600 cubic metres of raw biogas into green natural gas every hour. Once it is up and running normally, it will be able to produce this environmentally friendly fuel non-stop, i.e. 24 hours a day, 365 days a year. Over the long-term, Mainova and RMB are expecting to produce up to 30,000 megawatt hours of high quality biogas every year. An amount that will be able to cover the requirements of around 1,500 households.
“By transforming organic waste into natural gas, we are helping to push forward both environmental protection and the energy switch in our region.”
Aloys Oechtering, Managing Director of RMB
An exemplary project
“By transforming organic waste into natural gas, we are helping to push forward both environmental protection and the energy switch in our region. Thanks to the extension work carried out at the plant, this more sustainable form of recycling has also become more interesting from an economic point of view,” commented Aloys Oechtering, managing director of RMB and the manager responsible for biomass and bioenergy at REMONDIS. He is really pleased with the way the business has developed. It is, he says, an excellent project that clearly demonstrates how the creation of partnerships – for example with local energy providers – can ensure the very most is made of a region’s resources.
Image credits: image 1: © REMONDIS; image 2: Adobe Stock: David pix123