Towns and urban centres are effectively a huge store of raw materials. The UBA [Federal Environment Agency] has estimated that Germany’s infrastructure and buildings contain around 28 billion tonnes of raw materials. Urban infrastructure will have to be changed over the coming years, in particular due to climate change mitigation measures and the energy transition – and this will be felt by everyone. It is essential that the demolition work is carried out in a selective and orderly manner to ensure it is as resource friendly as possible.
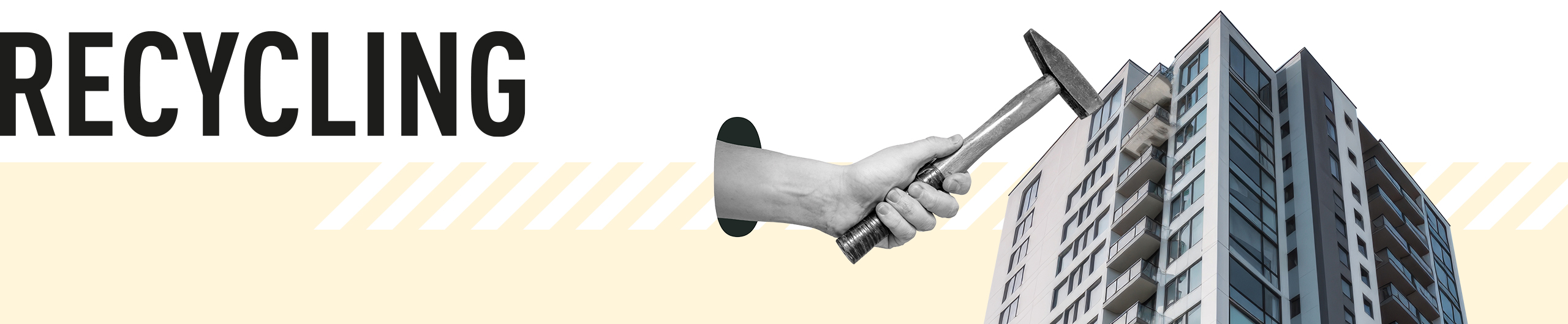
The pear-shaped, solid steel ball slams into the concrete wall with full force. A deafening noise breaks the silence whenever the driver of the digger directs the heavy wrecking ball against the building. Windows break, plaster flies through the air, the dust makes it difficult to breathe.
For decades, using a wrecking ball was the easiest and, supposedly, the most cost-effective way to get rid of worn-out buildings, dilapidated bridges and our building sins of the past. Knock them down, build something new and dump the construction waste at the nearest possible landfill: maximum efficiency for a linear economy – and for a world that had closed both eyes to the fact that our planet’s natural resources are finite. With climate change continuing to take hold, it will not be possible to simply carry on like this. Heavier rain events on the one hand and longer droughts on the other both highlight the downsides of prosperity – bought at the expense of the environment, throwing it out of balance. These weather events are testing urban infrastructure to the limit and forcing councils to adopt new measures, for example, intelligent rainwater management systems such as sponge cities. At the same time, the energy infrastructure of the fossil fuel age must be dismantled and rebuilt for renewable energies. Both effects will result in whole cities having to be redeveloped over the coming years to adapt to these new conditions.
Volumes of virgin raw materials used & mineral waste generated in the construction sector (in 1,000 tonnes)
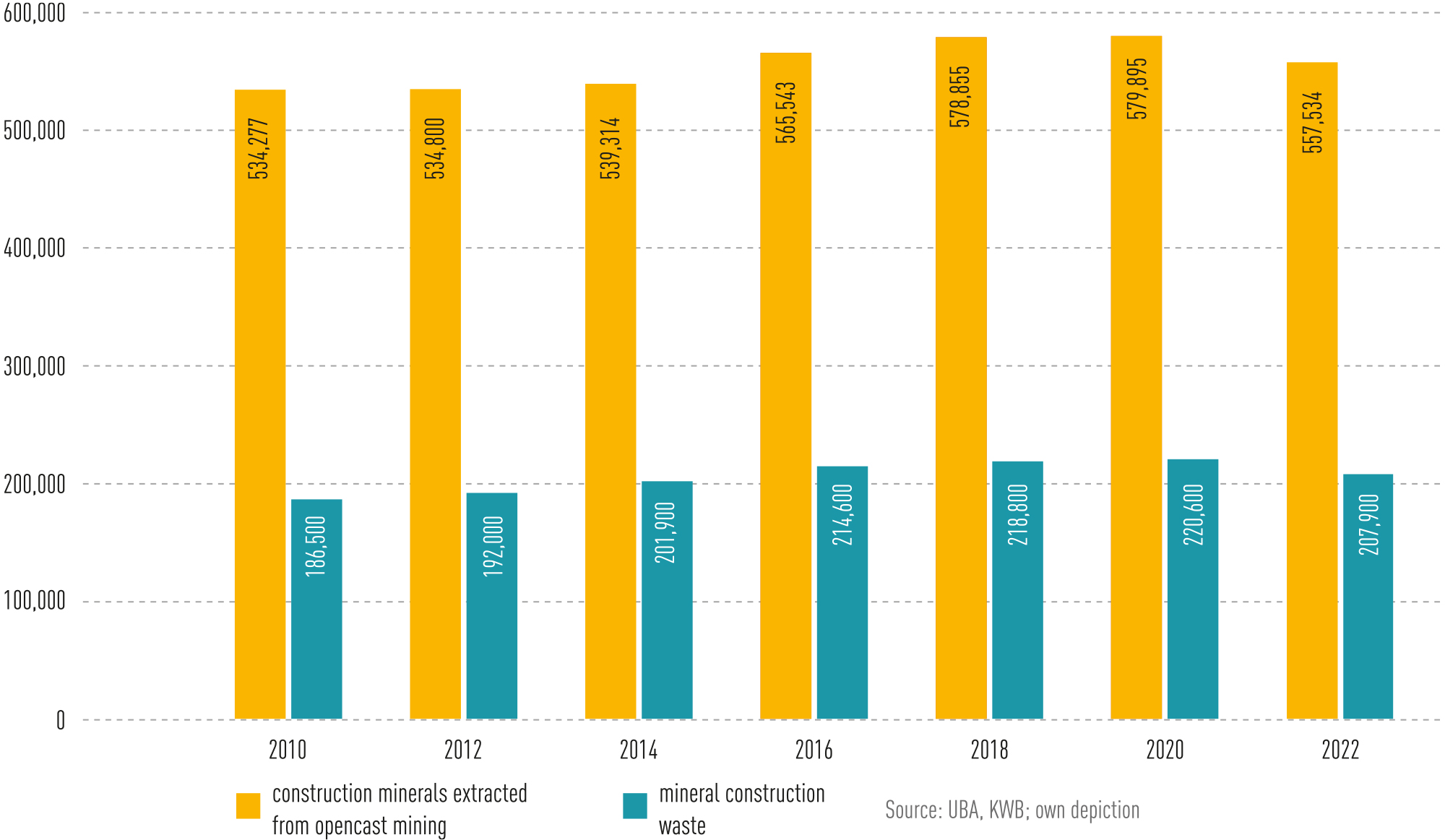
Ever more materials are being used
The UBA estimated that Germany’s infrastructure and buildings contained around 28 billion tonnes of raw materials in 2010. And more and more buildings are being added: according to the UBA, Germany mined around 557 million tonnes of virgin raw materials in 2022 to get the building materials it needed. Figures published by the KWB – a collaboration project of a number of associations in the construction sector and circular economy – show that around 208 million tonnes of construction waste were generated in the same year. The amount of material used to construct buildings in Germany, therefore, increased by a good 350 million tonnes in 2022 alone. If this figure is extrapolated and the estimated 28 billion tonnes from 2010 added to it, then the amount of materials contained in the country’s buildings and infrastructure must be around 33 billion tonnes in 2025.
Just how much of these must be dismantled and redeveloped to make buildings, roads and towns fit for the future and fit for our grandchildren is not yet clear. But it will be a big mountain to climb. The circular economy can help here to make the required redevelopments more sustainable. There is plenty of room for improvement though: according to the KWB, 90% of the 208 million tonnes of construction waste generated in 2022 was recycled. However, this is still far away from a circular economy. Why? Because a mere 13.5% of the aggregate needed at present is covered by recycled aggregate.
The amount of material used to construct buildings in Germany increased by a good 350 million tonnes in 2022 alone.
Selective demolition a must for efficient resource management
“We need to separate the different types of materials at building sites as cleanly as possible to increase the volumes of recyclable materials available,” commented Berthold Heuser from the REMONDIS Group company REMEX, which specialises in recycling construction waste. Wrecking balls are not able to generate such a homogeneous group of waste materials: according to data from the ‘Information System Built Environment’ (ISBE) run by the Leibniz Institute of Ecological Urban and Regional Development, around 90% of buildings are made up of mineral materials. Despite this large proportion, the remaining 10% are still enough to have all of the materials classified as non-recyclable or even hazardous. “Sorting them won’t help here either. The landfill is the only option left,” said Heuser.
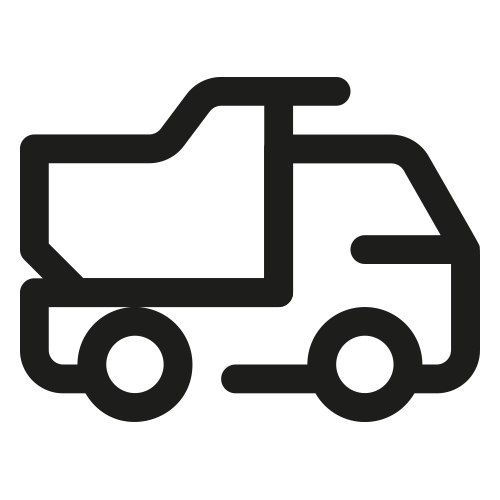
Construction waste is an excellent base material for REMEXIT as it is primarily made up of materials like concrete, bricks, tiles, asphalt, gravel and sand.
Furthermore, the German Commercial Waste Ordinance [GewAbfV] mandates selective demolition work and the segregated collection of the materials listed in the ordinance. These include, for example, glass, plastics, metal and timber. However, not all authorities enforce the German Commercial Waste Ordinance as strictly as they should: for years now, companies and associations operating in the circular economy have been criticising the fact that this ordinance is effectively not being enforced at all in many of the German states. “Unfortunately, it’s no different with construction waste either,” Heuser said. Some German states – such as Brandenburg – have published guidelines on selective demolition. But these are no more than a recommendation and are not legally binding.
One problem is that there are still no mandatory rules about how buildings must be demolished. According to information published by the DA [German Demolition Association], the statutory regulations primarily originate from general waste hierarchy rules and the sorting regulations set out in the German Circular Economy Law [KrWG].
Statistically recorded volumes of mineral construction waste in 2022 (in million tonnes)
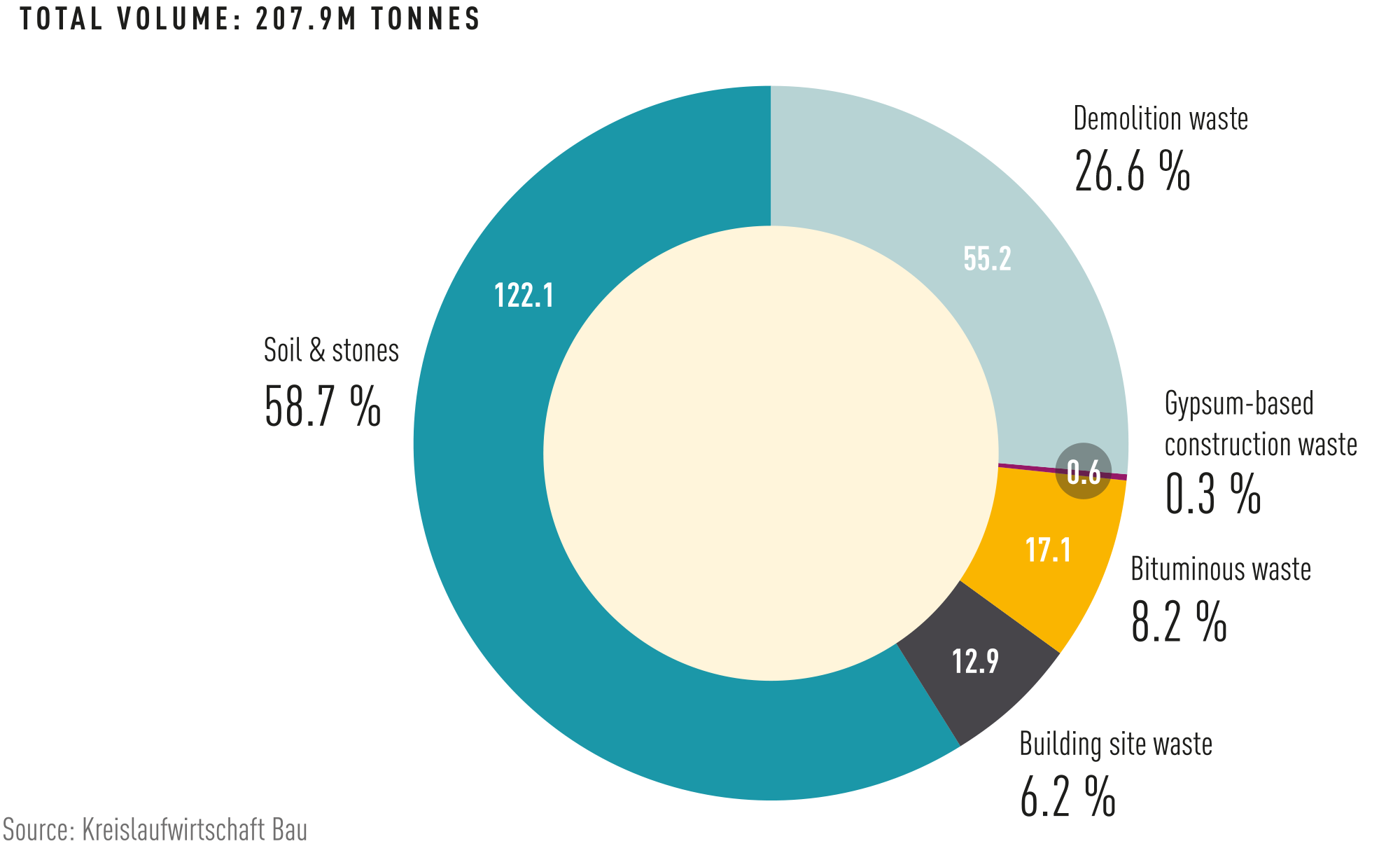
REMEX’s substitute product REMEXIT demonstrates what can already be done today with mineral materials generated from selective demolition work. The recycling plants operated by REMEX use the waste collected from building and road construction projects to produce REMEXIT. Every year, REMEX produces more than two million tonnes of recycled aggregate at its 20+ facilities.
“Construction waste is an excellent base material for REMEXIT as it is primarily made up of materials like concrete, bricks, tiles, asphalt, gravel and sand,” explained Heuser. Modern screening and selection procedures are used during the recycling process to produce different particle sizes. These are then combined with specific amounts of the various types of REMEXIT aggregate, which are particularly suitable for road construction and earthwork projects thanks to their positive physical properties. REMEXIT is, for example, well suited for use in frost protection layers and gravel load-bearing courses in all categories of road – including motorways.
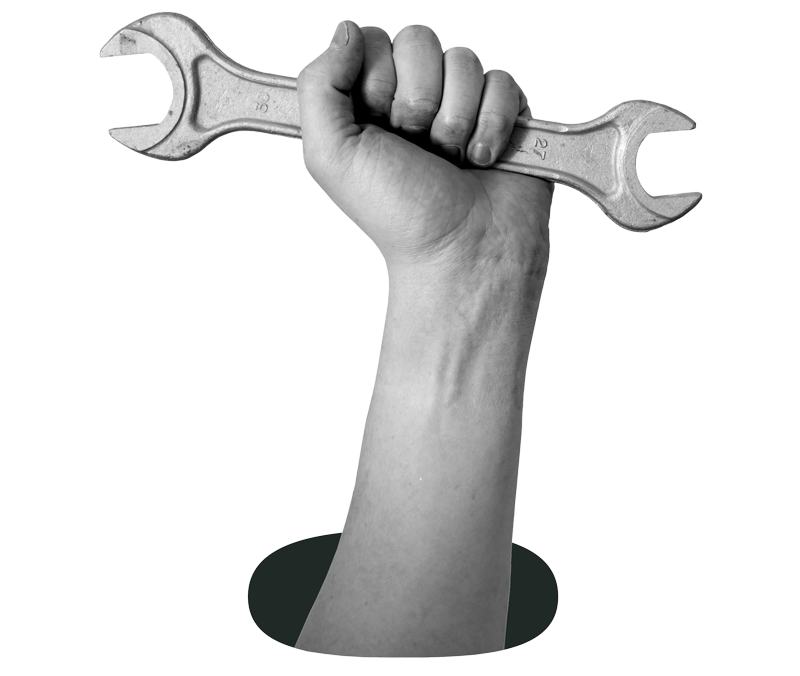
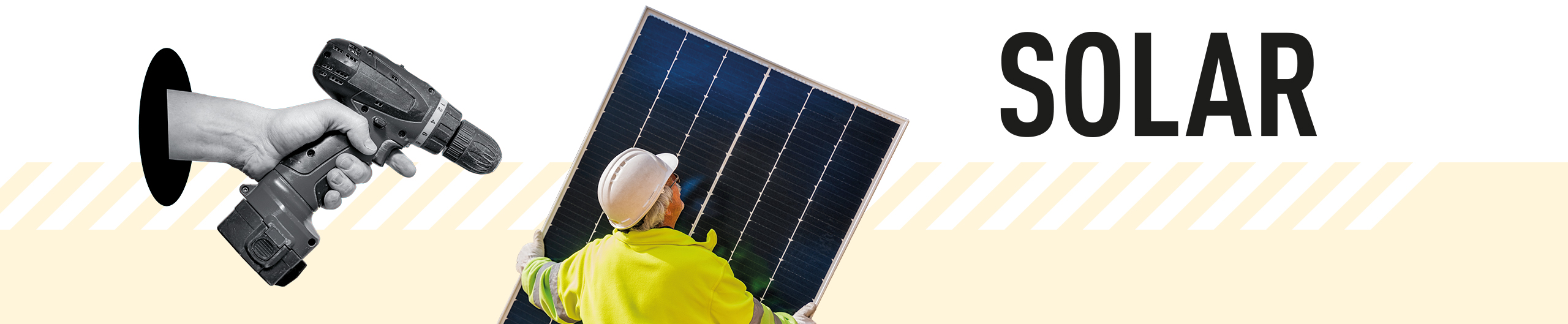
Solar modules: high-quality raw materials require selective demolition
Even though minerals easily make up the biggest waste stream generated by the construction sector – both from point of view of weight and volume – this does not mean that the other materials play less of a role. Decommissioned solar PV systems are growing in importance because of their raw material contents (such as silicon, silver and copper). “The number of old solar modules being returned is not good,” commented Tim Wilms, managing director of REMONDIS Electrorecycling GmbH, a TSR Group company, referring to the figures published by EAR (Stiftung Elektroaltgeräte Register). According to these numbers, companies manufacturing and selling PV systems installed over 800,000 tonnes of solar panels on the roofs of private households in 2023. However, a mere 2,000 tonnes of panels were returned for recycling via EAR’s collection scheme in the same year. “The solar panel market is still ramping up, especially in the B2C sector. This means that there is bound to be a certain discrepancy between the input and output volumes,” Tim Wilms explained. Having said this, the numbers being returned are so low that many experts are puzzling about their whereabouts – and are assuming that some PV modules are ending up in the skips containing mixed construction waste instead of on the segregated piles of materials. “The problem here is that hardly anyone is prepared to build a recycling plant for these materials when the volumes are so low,” Wilms continued.
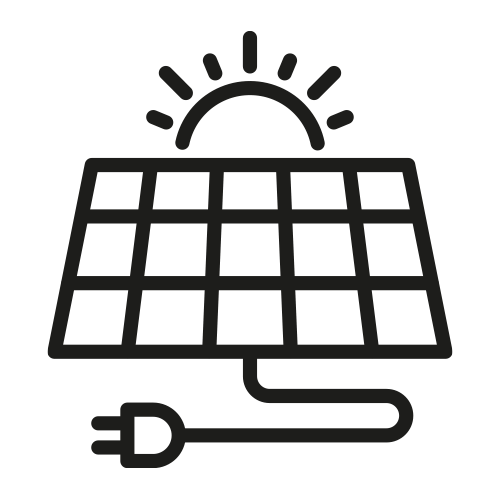
Companies manufacturing and selling PV systems installed over 800,000 tonnes of solar panels on the roofs of private households in 2023.
The age-old problem of the chicken and the egg: no one will set up a recycling plant when the volumes are so low – and everyone questions why such panels should be collected separately if there are no recycling plants around to process them. REMONDIS Electrorecycling is now taking steps to break this vicious circle as so many natural resources are being wasted – and it is sticking very closely to the waste hierarchy here. “We opened up a plant in Lünen last September that carries out checks on old solar panels to see whether they can be reused,” Tim Wilms explained.
At the end of the day, PV modules with a residual capacity of over 150 watts can generally be used again. “Besides carrying out this performance test, we also do a so-called hipot test. This enables us to check whether the panels are still suitable for high voltages,” Wilms continued. Furthermore, checks are also carried out to make sure none of the glass is damaged. “Once all the checks have been completed, the device is given an inspection number and can be sold on to a dealer.”
At some stage or other, though, all solar panels will reach the end of their useful life. The only thing of value that these old panels still have is their raw material contents. Even if the volumes are low at the moment, experts expect there to be a flood of old solar panels in the future – panels that can no longer be reused and need to be recycled to secure raw materials for Europe’s industry. The International Energy Agency, for example, has estimated that up to one million tonnes of old PV panels will be available for recycling in Germany alone in 2030. And this figure is expected to rise to 4.3 million tonnes in 2050.
REMONDIS Electrorecycling intends to use its own recycling capacities to make sure that the raw materials in the old panels undergo high-quality recycling so they can be returned to market for reuse. Which is why its Dutch subsidiary MIREC commissioned a recycling plant last November that is dedicated to recovering the material contents of defective panels and recycling them for reuse. “The facility removes the aluminium frames, the PV system’s plug-in box and the glass parts so that the individual types of material are separated from each other. Thanks to this recycling solution, over 80% of the input weight can be sent for materials recycling,” Wilms said. Plans are to further optimise the plant in the future to increase this recycling rate to 90%.
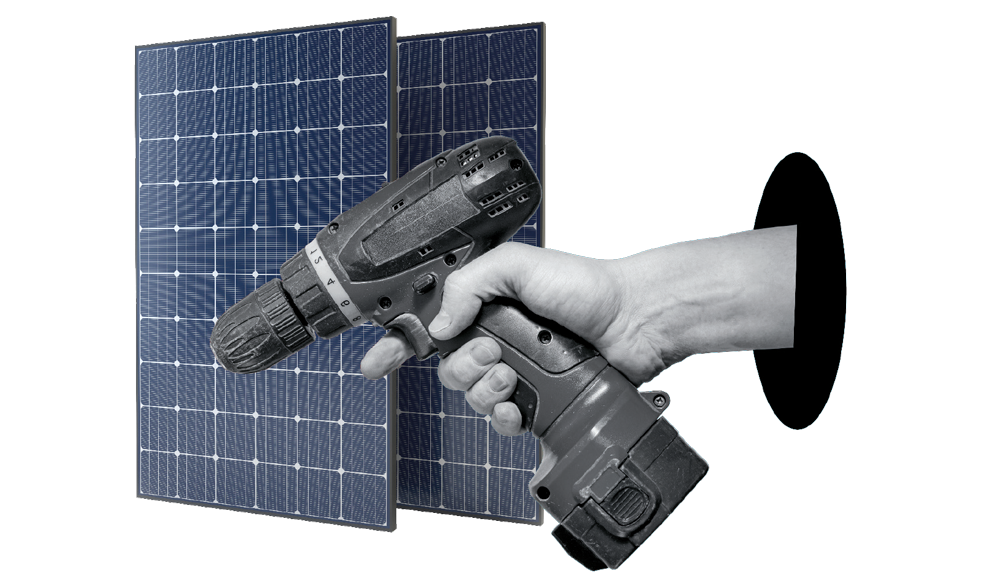
And yet Wilms remains worried about the low return rates. “We offer a variety of storage and transport options to increase the amount collected,” the managing director of REMONDIS Electrorecycling said. Its sister companies within the REMONDIS Group can then use these to segregate the PV panels when a building is being demolished. “The transition towards using recycled rather than virgin raw materials will only be a success if everyone joins in,” Wilms concluded.
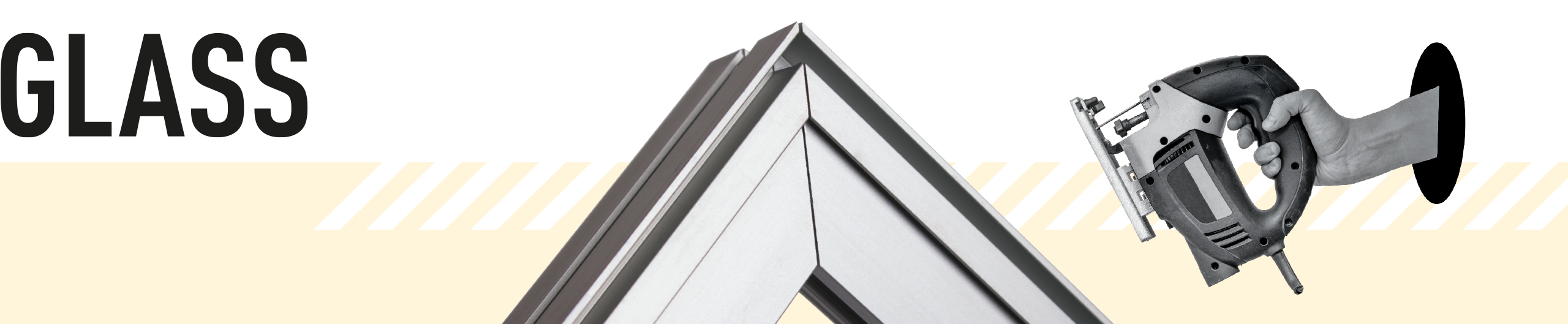
Glass recycling: it’s all about purity levels
The glass that REMONDIS Electrorecycling recovers from the old solar panels is recycled within the REMONDIS Group. “80% to 90% of a solar panel is made up of glass depending on the model,” commented Christoph Bildstein, managing director of REMONDIS Recycling. If the solar panels are segregated cleanly from the other materials at the demolition site, then this glass is perfect for recycling.
It is considerably more difficult to recycle windowpanes that have been removed during a building demolition or renovation project if they have been contaminated with other residual materials – i.e. if they have not been cleanly segregated from the other substances, in particular minerals, at the building site. Even the smallest mineral particles can cause problems if they remain stuck to the glass despite careful processing. These deposits can lead to bubbles forming when the glass is melted down at temperatures of between 1,200°C and 1,300°C during the production process, which can affect the stability of the windowpane depending on its size. In any case, such bubbles certainly have an impact on the way the glass looks and makes it more difficult to see through.
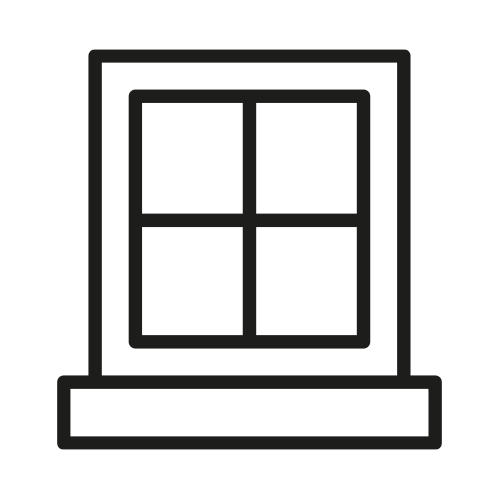
A joint working group organised by the two circular economy associations, BDE and bvse, estimates that the volume of windowpanes that could potentially be recycled each year lies at around 100,000 tonnes.
“This is the reason why the flat glass industry has been holding back when it comes to requesting recycled glass,” Bildstein continued. This all has to do with the standard production process used by the sector: flat glass is made using the float glass process that effectively creates an endless ribbon of glass that is then cut up at the end. If bubbles are in the glass then the loss is relatively great. Which is why recycled glass from the building sector is normally used in other production processes.
And yet the interest in recycled raw materials is growing in the flat glass industry as well. Tests are currently being carried out in the industry to increase the recycled content of flat glass. These efforts are being made by manufacturers in order to cut their carbon emissions and so improve their carbon footprint. However, it is not possible at present to provide the industry with figures to illustrate the market potential here.
“There are simply no reliable figures available about the volumes of old glass generated by the building sector,” Christoph Bildstein explained. Lax enforcement of the statutory regulations – in particular of the German Commercial Waste Ordinance – is playing a role here, too: as the authorities in many of the German states tend to turn a blind eye to what is going on in this area, large volumes of recyclable materials are ending up in the piles of mixed construction waste and being sent for incineration. “No one is recording the data because this data can’t be recorded under such conditions,” Bildstein concluded. A joint working group organised by the two circular economy associations, BDE and bvse, estimates that the volume of windowpanes that could potentially be recycled each year lies at around 100,000 tonnes. A mere 25,000 tonnes of this, however, actually reaches recyclers.
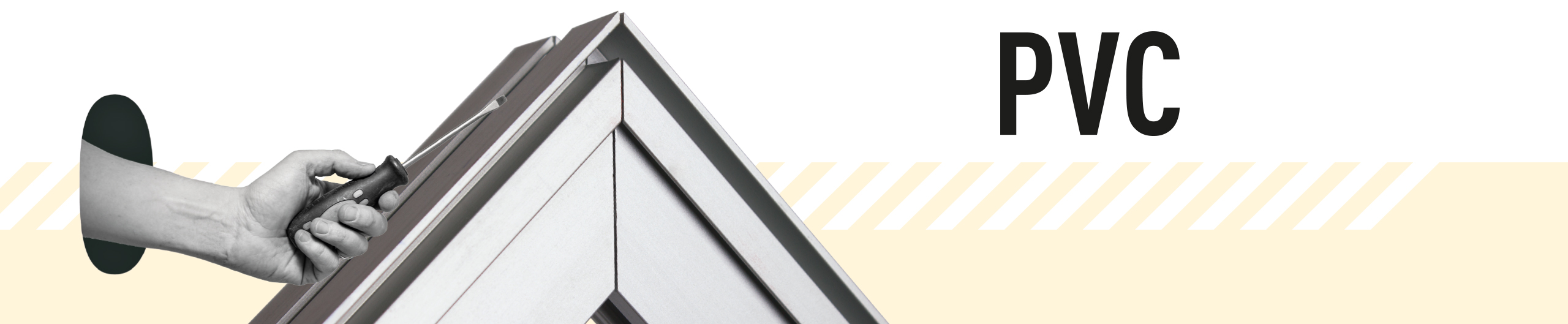
Recycling PVC window frames: untapped potential
Wherever there are windowpanes, there are also window frames – normally made of aluminium, wood or plastic. Window frames made of polyvinyl chloride – a plastic better known as PVC – are a very good material for recycling. “The challenge here is the volumes available,” commented Mario Husemann, one of the two managing directors at RE:CORE. The Rewindo network puts the gross potential volumes of old windows, blinds and doors across the country in 2023 at just under 67,000 tonnes.
RE:CORE is a joint venture set up by the REMONDIS Group and the building envelope specialist Schüco. The goal of this joint venture is to promote the recycling of old PVC building parts by creating numerous partnerships at a variety of levels. “The fact that RE:CORE is itself a joint venture is really useful here,” Husemann said. “Why? Because this long-term partnership unites the core areas of expertise of both companies in the best possible way, enabling it to drive forward the creation of a circular construction sector that has a reliable supply of environmentally and climate-friendly raw materials in the future.” According to Rewindo, every tonne of recycled PVC saves two tonnes of CO2 and 16,400 kilowatt hours of electricity compared to the production of new products.
However, to be able to tap into this potential, it is essential that the old windows
are segregated and stored separately from the other materials when the buildings are being demolished. Partnerships and collaborations are being set up at the building sites to make it easier to segregate the materials and generate high-quality mono-fractions. “REMONDIS has a waste management logistics network that covers the whole of Germany,” Husemann explained. “We use this network to collect and transport old window profiles separately.” By offering this service, RE:CORE wishes to make it as easy as possible for its partners to hand over their old PVC material so that it can get hold of large volumes and pass these on to the circular economy. What’s more, RE:CORE is also able to accept small volumes of material from tradespeople, small construction companies and even private households when they carry out house demolition or renovation projects.
But all of this is not enough on its own. Which is why RE:CORE has also been listed as a partner at Rewindo since the middle of October. In addition to this, RE:CORE is looking to further expand its network of partners as well. “The more closely knit our partner network is, the more efficient our circular economy operations – i.e. the logistics, processing, recycling and use of recyclate – are,” Husemann concluded.
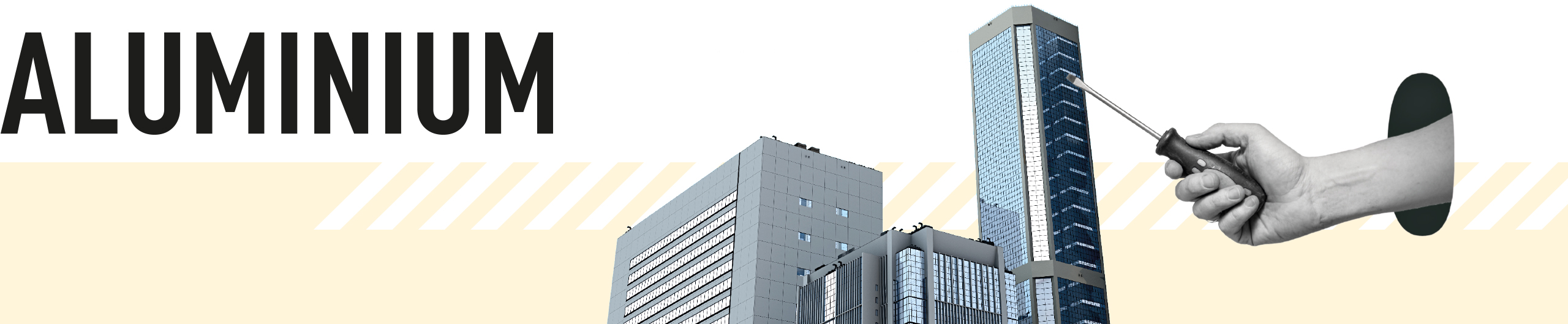
Aluminium window frames: recycling saves energy & improves carbon footprints
Building demolition work, however, not only generates window profiles made of PVC. Around a quarter of all window frames and facade parts installed in buildings in Ger-many are made of aluminium. For a long while, this metal was considered not to be a good option for windows, in particular because of heat loss. Compared to plastic and wood, aluminium has very high thermal conductivity and tended to transfer heat from the inner face of a frame to the external face, especially during the colder months of the year. “Modern aluminium window frames are equipped with thermal breaks, i.e. with an insulating barrier made of polyamide and polyurethane. These prevent heat being transferred from the inside to the outside of buildings,” explained Marcus Kröger, project manager for aluminium recycling at Schüco International KG. Schüco offers holistic solutions for sustainable building envelopes. Thanks to the way aluminium is used in building parts, the potential for setting up a circular system here is huge as the metal can, for the most part, be recycled endlessly.
The carbon footprint of a window frame made from virgin aluminium is also significant as the process needed to produce this metal from bauxite ore is incredibly energy intensive. “Recycling has a clear advantage here,” said Tim Holtmann from REMONDIS’ TSR Group. “Using recycled raw materials not only conserves natural resources. It also reduces carbon emissions and cuts energy consumption compared to the production processes using virgin raw materials.”
The carbon footprint of aluminium window profiles will play an ever more important role in the construction sector in the future. The EU’s Energy Performance of Buildings Directive, which came into force in April last year, obliges building owners and construction companies to calculate and declare the life-cycle global warming potential of new buildings from 2030 onwards. This means that they must not only take the carbon emissions generated from operating the building into account but also the carbon footprint of the materials used to construct it. Window profiles made of virgin aluminium will clearly have a negative impact here.
“The potential for setting up a circular system for aluminium is huge.”
Marcus Kröger, Project Manager for Aluminium Recycling at Schüco International KG
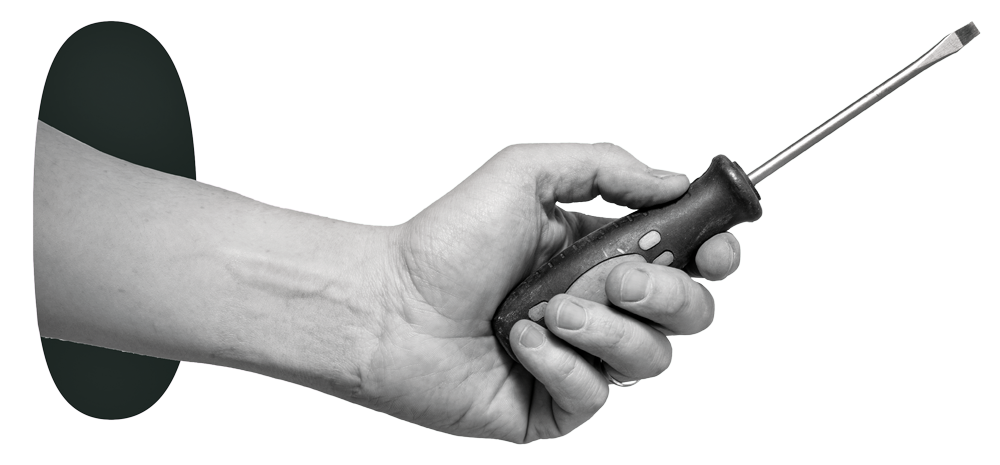
Recycled raw materials could be used instead but they must be of the right quality. “Here at the TSR Group, we have a high-quality recycled raw material called TSR136 in our portfolio that meets the very high demands of numerous industrial applications. This enables manufacturers to considerably increase the recycled content of their products,” Holtmann explained. Kröger corroborated this statement and added: “Our suppliers can use TSR136 as a base material without having to process it beforehand.”
And it is precisely this recycled raw material that should help to further reduce the carbon footprint of aluminium window profiles in the future. To be able to offer the market this eco-friendly alternative, TSR and Schüco are working on a take-back scheme to tap into this source of raw materials from the building sector. Their goal is to recover old windows and facades made of aluminium from demolition and renovation projects and use this material to make TSR136.
It was for this reason that RE:CORE metals GmbH was founded to enable the range of recycling services to be offered by just one company. TSR136 will then be used to produce new window profiles.
Schüco markets these window profiles, partly made using TSR136, as ‘ultra-low carbon’. “Our ultra-low carbon aluminium window profiles considerably reduce a building’s carbon footprint without compromising on the quality of the product at all!” Kröger explained. “Instead of the 7.11 kilograms of carbon produced per kilogram of aluminium profile, our ultra-low carbon products generate a mere 1.99 kilograms of carbon per kilogram of aluminium profile – which means that a building built with 40t of ULC profiles rather than standard profiles cuts carbon emissions by 200 tonnes!”
A closed loop that helps curb climate change – and that works best when the old materials are cleanly segregated and stored separately from the other materials at the building site. “We and our partners are, therefore, doing a lot of explaining here – telling window installers, demolition firms and construction companies about how important this is,” Holtmann continued. They wish to raise awareness about the importance of segregating the different materials. Tenders put out for large projects are more likely nowadays to address the issue of segregating window profiles and recycling the material so it can be returned to market. This helps to promote the separate collection of the input material.
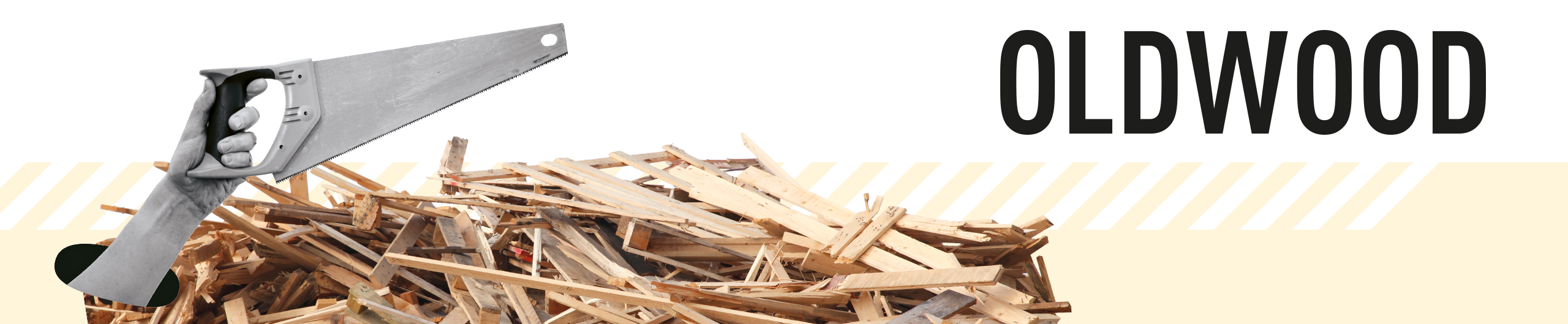
Old wood – local, net-zero bioenergy
Old timber generated at building sites can also be put to good use and recycled – if it is segregated and stored separately from the other materials at the construction site. In general, the volumes of old wood are subject to economic cycles like so many other types of material. “Germany’s current economic situation means that around eight million tonnes of waste timber are generated in the country each year,” explained Annette Hansberg, plant manager at REMONDIS Holzaufbereitung GmbH, Rhein-Wupper. This company’s tasks include managing timber recycling across large parts of the Rhineland. “When the economy is running well, then this figure can rise to 10 million tonnes or more,” Hansberg continued. According to a study published by Münster University of Applied Sciences on behalf of the UBA, around 26% of waste timber comes from the construction sector. “What we don’t know, though, is how much of this is from demolition work.” There is a distinct lack of data here – just like with the other materials.
Old wood generated from demolition projects is, for the most part, used to produce energy in biomass-fired power plants. This can be put down to the specific way that construction wood is treated. “Construction timber has often been treated with chemicals to protect it against fungal infections or make it less flammable,” Hansberg explained. Such chemical treatment makes the wood more durable but also reduces the options available to recycle it. “One problem here is that it’s not possible to see whether the wood has been treated or what is has been treated with simply by looking at it.” Construction wood is, therefore, normally thermally treated in Germany as a precautionary health protection measure as well as to protect clean wood that has been earmarked for recycling.
Using old timber to generate energy in biomass-fired power plants is, however, no less sustainable. “Construction wood from demolition projects has often been in the buildings for 50 years or more. The wood that was once used has grown back during this period.”
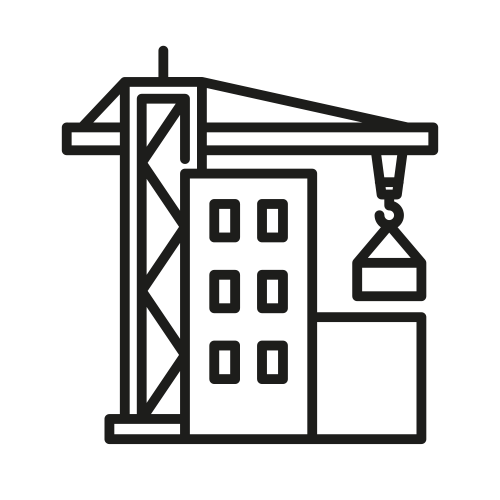
According to a study published by Münster University of Applied Sciences on behalf of the UBA, around 26% of waste timber comes from the construction sector.
Waste wood in 2016 acc. to Germany’s waste statistics, divided up into sectors
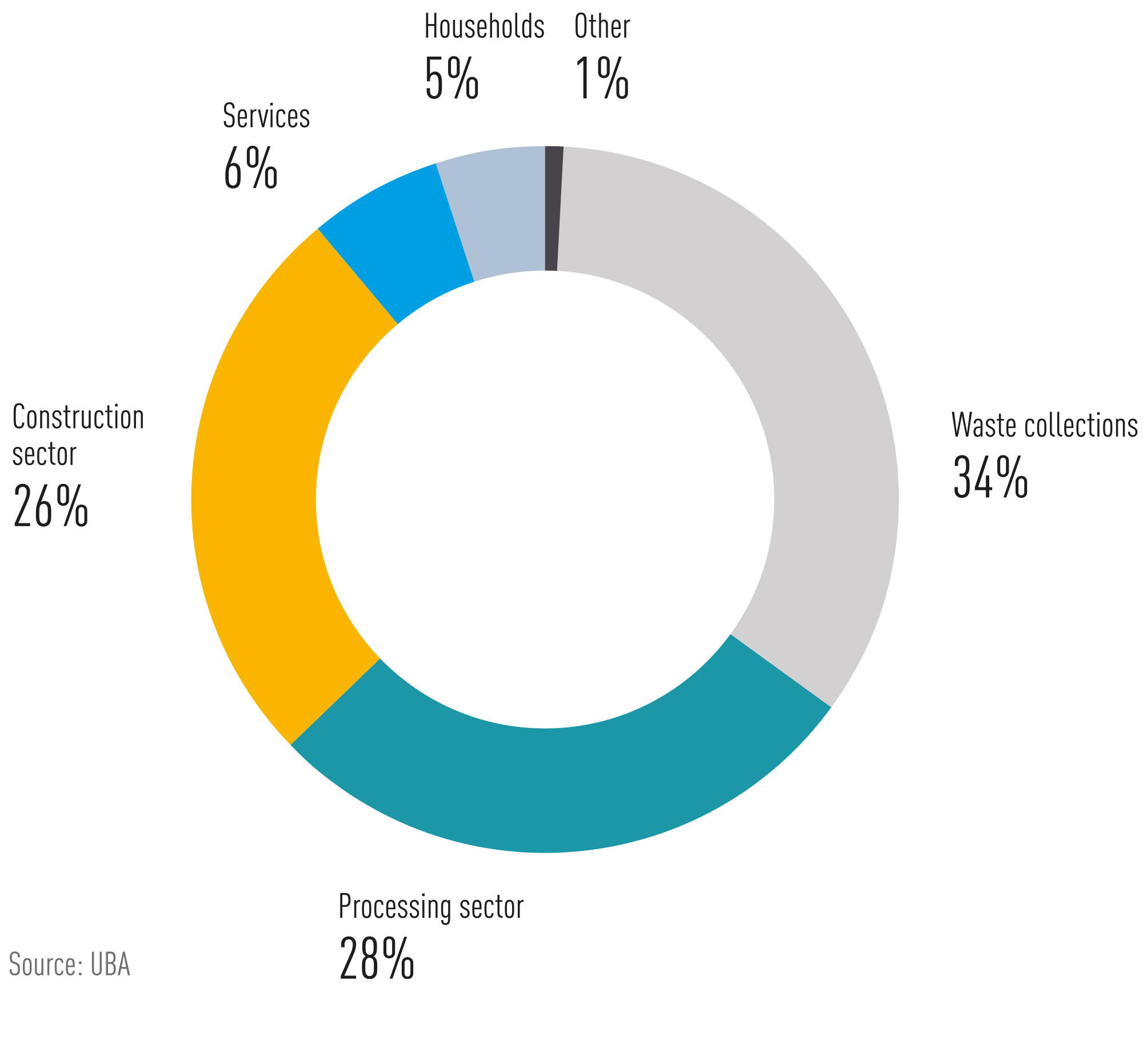
The energy generated by this old timber helps local authorities, industry and energy providers to implement both the energy transition and heat transition. Old wood is a climate-neutral fuel that is available locally – and that is in high demand: the thermal recycling capacities available on the market have already exceeded the volumes of old wood available. On top of this, many new biomass-fired power plants are currently being planned or built. “The demand is most certainly there,” Hansberg said. This is something that is also reflected in the price: “There is a noticeable difference in the cost charged per tonne for thermally treating mixed construction waste at a waste incineration plant and for thermally treating cleanly segregated old wood from selective demolition projects at a biomass-fired power plant,” Hansberg continued. “We pass on this financial incentive to our own customers of course.”
This means that it is certainly worth their while for construction companies to ensure the different waste streams are cleanly segregated and stored separately at their building sites. No matter whether it be old wood, minerals, e-waste (such as solar panels), windowpanes or aluminium and PVC window frames: it is much cheaper for firms to dispose of these materials if they have already been pre-segregated at the construction site. Selective demolition is good for the climate, conserves natural resources, increases resilience and saves costs. The segregation and separate storage of construction materials is the first – and most fundamental – step required to set up a well-functioning circular economy in the construction sector. The best place for the wrecking balls, therefore, is in a museum – or to send them away to be recycled.
“Germany’s current economic situation means that around 8 million tonnes of waste timber are generated in the country each year.”
Annette Hansberg, Plant Manager at REMONDIS Holzaufbereitung GmbH, Rhein-Wupper
Image credits: image 1: Adobe Stock: beast01, sizsus, DSN_1, Mathias Weil; image 2: Adobe Stock: OMD, beast01; image 3: Adobe Stock: beast01; image 4: Adobe Stock: Javier De La Torre/ADDICTIVE STOCK, beast01; image 5: Adobe Stock: beast01, Studio Harmony; image 6, 7: Adobe Stock: beast01, Maksim; image 8: Adobe Stock: philipk76; image 9: Adobe Stock: Mathias Weil, beast01; image 10: Adobe Stock: beast01; image 11: Adobe Stock: detailfoto, beast01