Processes are setting new standards
What is the best way to recover as many metals as possible from incinerator bottom ash (IBA)? This is a question that recycling specialists across the world have been looking to solve. The answer has been found by REMEX GmbH, a company belonging to the REMONDIS Group. It is setting new standards with its smart metal recovery technology, MERIT®, that it unveiled just recently.
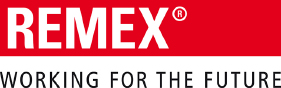
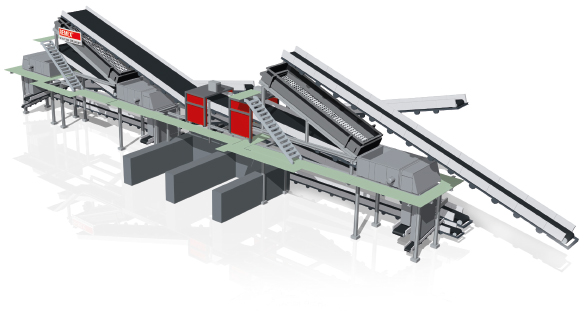
REMEX’s series of 3D animations show how the different metals are recovered and processed: remex-processing.com
Now possible to recover very small pieces of metal
MERIT® is a system that has been developed thanks to REMEX’s international research and development activities. This innovative technology, whose name derives from the term “metal recovery intelligence”, is already being used in a number of REMEX’s recycling facilities. The biggest advantage of this process: even the smallest pieces of non-ferrous metal (two to four millimetres in size) can now be filtered out of the IBA. Conventional treatment plants do not recycle these very small particles because they do not have the technology able to do this.
REMEX is the market leader in both Germany and the Netherlands for processing IBA.
The volumes of non-ferrous metals (such as aluminium and copper) able to be recovered can now be greatly increased thanks to MERIT®. What’s more, the system is environmentally friendly and cost effective as it improves the quality of the recovered metals. Not only REMEX’s customers benefit. Other recycling businesses can also make the most of this innovative technology via cooperation agreements.
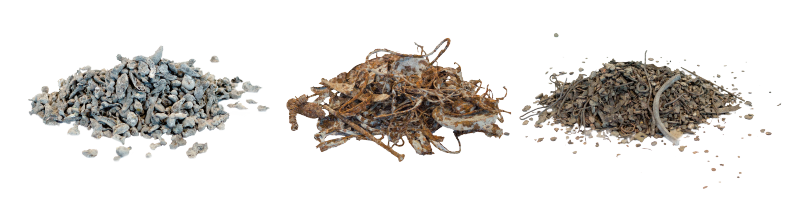
An international role model in the Netherlands
HEROS Sluiskil B.V., a company situated in the south west of the Netherlands, demonstrates perfectly how the new MERIT® technology can be used. A subsidiary of REMEX-Mineralstoff GmbH, this firm operates Europe’s largest IBA treatment plant, handling around 700,000 tonnes of IBA every year.
Every year, REMEX handles more than 2.5 million tonnes of IBA in its recycling plants – a volume equivalent to the household waste generated by ca. 23 million people.
A modern metal treatment facility was also built at HEROS’ site in Sluiskil at the same time the MERIT® technology was introduced. This facility focuses on cleaning and sorting non-ferrous metal concentrate from REMEX’s recycling plants so that it can be returned to production cycles and reused. The concentrate travels over an air conveyor containing a number of different sieves so that the non-ferrous metal can be separated into light and heavy metals. The end product: high-purity metal fractions that can be sent straight to foundries for reuse – further processing is not necessary.
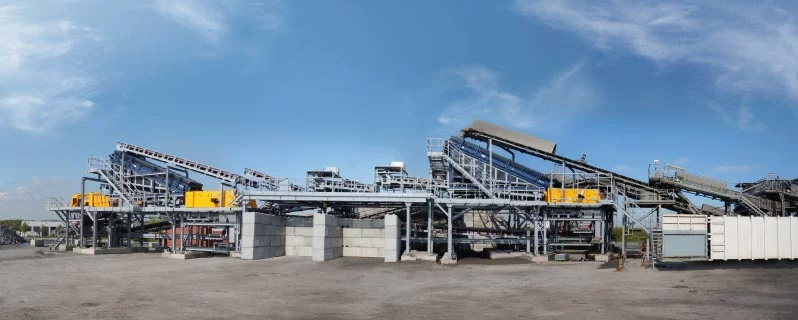
The goal: 100% recycling
This is not the first time that REMEX has succeeded in developing the technology it uses to improve metal recovery rates. When producing its quality-assured aggregate (granova®) from IBA, for example, it is able to recover around 90 percent of the ferrous and non-ferrous metals contained in the ash. These metals are then processed so they can be returned to production cycles. The company continues to set itself ambitious targets, as REMEX managing director Michael Stoll explained: “Our overall goal is to operate a system that makes 100% recycling possible – where smart technology enables absolutely all resources to be recovered and reused.”
REMEX links its international locations
REMEX is also expanding its activities in Asia. This August, the company’s facility in the Malaysian city of Pasir Gudang began processing metals recovered from incinerator bottom ash (IBA). These ferrous and non-ferrous metals are being supplied by REMEX’s metal recovery plant in the neighbouring country of Singapore, which was built back in 2015 and processes around 1,600 tonnes of IBA every day.
Image credits: © REMEX