Besides the mega industrial recycling centre that the REMONDIS Group operates at the Lippe Plant in Lünen, it also has a further 1,000+ business locations situated across three continents. Which means, of course, that a ‘one size fits all’ approach won’t work when it comes to the subject of energy management. Just because one site has found the right solution for their business certainly doesn’t mean that it will work elsewhere. REMONDIS’ largest regional company is based in the Rhineland around Cologne and Düsseldorf and has around 40 different sites. One thing in particular is bothering Reinhard Hohenstein, managing director of REMONDIS Rhineland, at the moment: the long delays that they are having to put up with to get their new photovoltaic (PV) systems up and running. With three such systems currently in the starting blocks, the company will be using most of the electricity produced to cover its own needs.
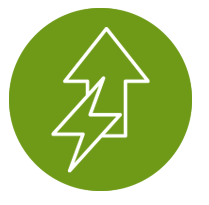
This regional company, with its approx. 2,400 employees, was not unprepared for the increase in energy prices at the beginning of 2022.
It has been running an energy management system in line with ISO 50001 for over 10 years now. This accreditation aims to help companies continuously improve their energy consumption by providing them with data that they can then use to optimise their facilities and machinery – something that is particularly important when energy prices are skyrocketing. One key factor here is understanding exactly how operating times and capacity are controlled to avoid maximum demand. Once this is clear, energy consumption can then be structured so that the various plants and facilities remain cost effective. By doing just this, the company was able to make sure that none of its machines had to be shut down completely.
While supplies of electricity, gas and heat were able to be secured during the critical period between autumn 2022 and spring 2023, Reinhard Hohenstein stressed that the current prices are still too high: “Being part of a large group, we don’t really benefit from the energy price cap.” On the other hand, belonging to such a group does provide cost advantages as its centralised energy procurement measures create economies of scale – at least they do in a normal market environment.
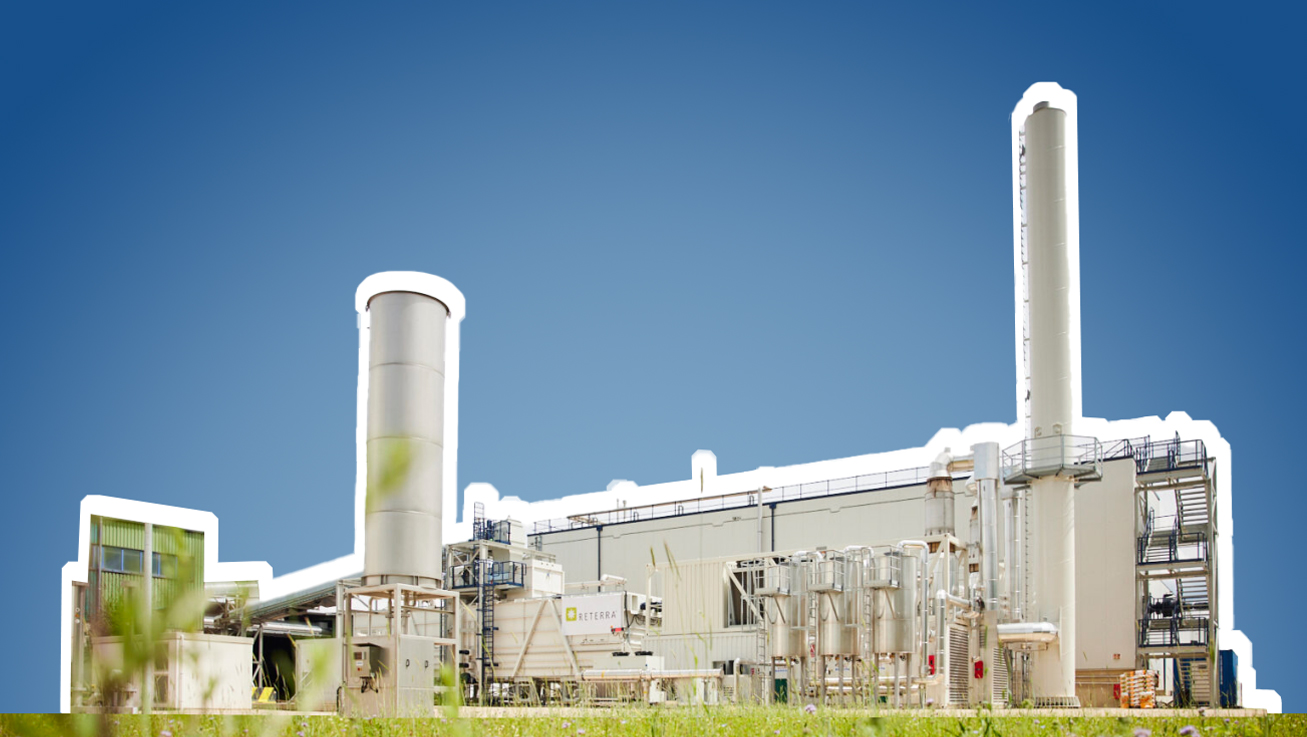
One effective way for a company to stem rising energy costs is to produce its own electricity. REMONDIS’ business in Erftstadt (its second-largest site after Lünen) operates a digester for organic waste that also produces biogas, which is then transformed into electricity on site in a combined heat and power plant.
Focus is also being put on solar power. At the moment, Erftstadt’s PV system has a peak output of around 750 KW and the new systems due to be installed in Troisdorf and Chorweiler will each add a further ca. 1,300 KWp. Supply bottlenecks at the manufacturers, however, have meant that these projects have been delayed. And Hohenstein mentioned another problem: “It’s crucial that the electricity grid is expanded more quickly so that solar power can be used. Our PV systems are already being switched off regularly by the grid operators as the network is overloaded.” REMONDIS primarily uses the electricity produced by its PV systems to cover its own needs – approx. 80% of output. Making such investments cost effective, however, also includes factoring in additional income from selling the excess electricity.
More and more of the country’s electricity should be produced from renewable energy over the coming years – something that is also important if the carbon reduction targets are to be reached. What’s more, the country is also looking to reduce its dependency on natural gas. REMONDIS Rhineland has, therefore, begun a project to switch the technology being used to clean the waste gas after the anaerobic digestion process to UV oxidation. The results have been positive so far even if the management team and staff at REMONDIS Rhineland still have a long way to go.
In the spotlight: the Merkenich paper sorting plant
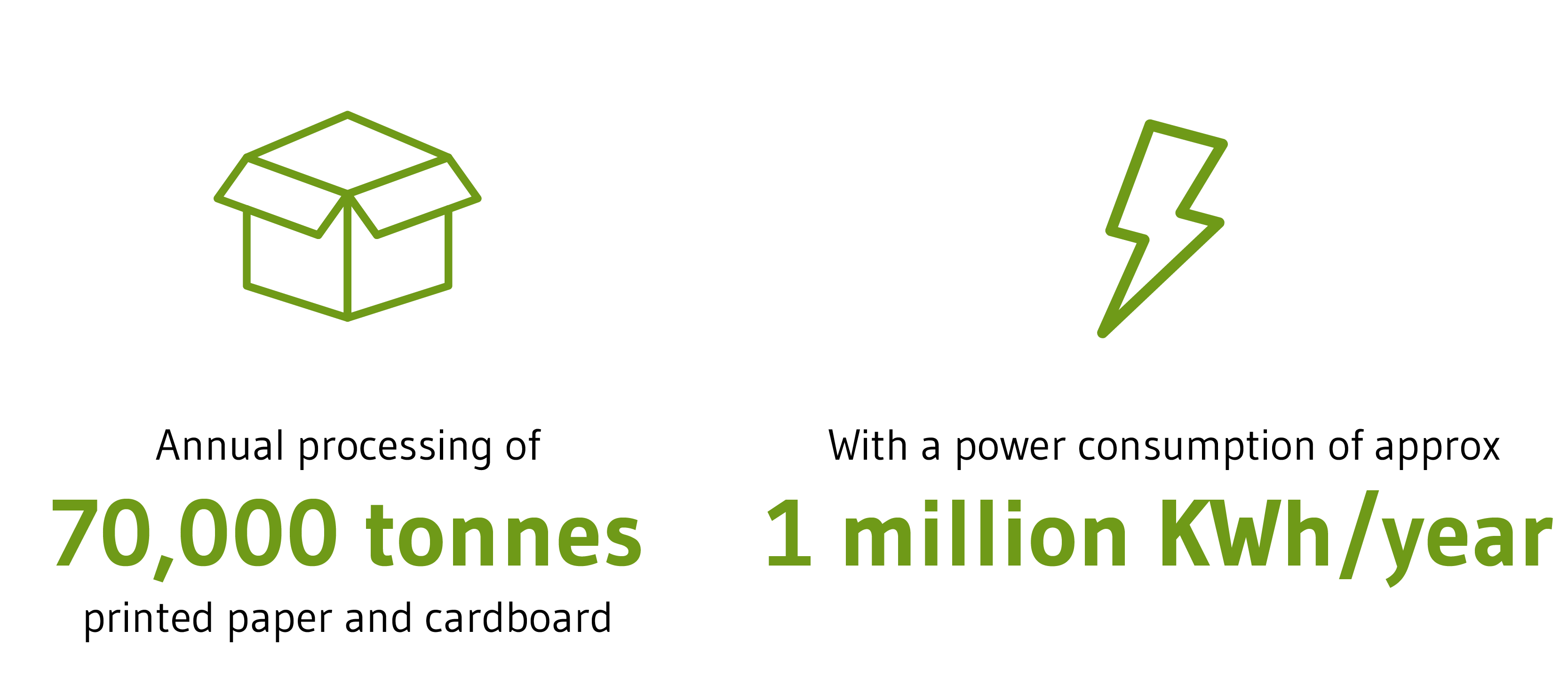
The paper sorting plant in Cologne’s district of Merkenich is an excellent example of how an energy management system can be implemented. Situated on the left of the River Rhine, this REMONDIS plant sorts paper and cardboard. Each year, it handles around 70,000 tonnes of printed paper and cardboard so that the material can be reused in paper mills. Its operations consume around 1 million KWh of electricity every year.
Most of the material it handles comes from the City of Cologne; the rest is processed on behalf of other recycling firms. The material is sorted into three different fractions: mixed paper, cardboard, and paper for deinking. The 16 members of staff run the plant using a two-shift system, Mondays to Fridays.
In order to lower its electricity costs, the company decided to implement a comprehensive electricity measuring concept back in 2015 by installing smart meters that transmit their data to a central software programme. “Where does the electricity actually go? That might sound like a trivial question but in fact many manufacturing companies in Germany still don’t know exactly how they consume electricity,” said plant manager Thomas Römbke, describing the challenges faced by businesses. They know the overall amount of electricity they consume from the central meter installed by their energy provider. But if they don’t know how much energy each individual process consumes – from their operating power to their compressed air, from their lighting systems to their heating systems – then they can’t really check whether the investments they make in energy-saving measures are cost efficient nor can they effectively control their consumption.
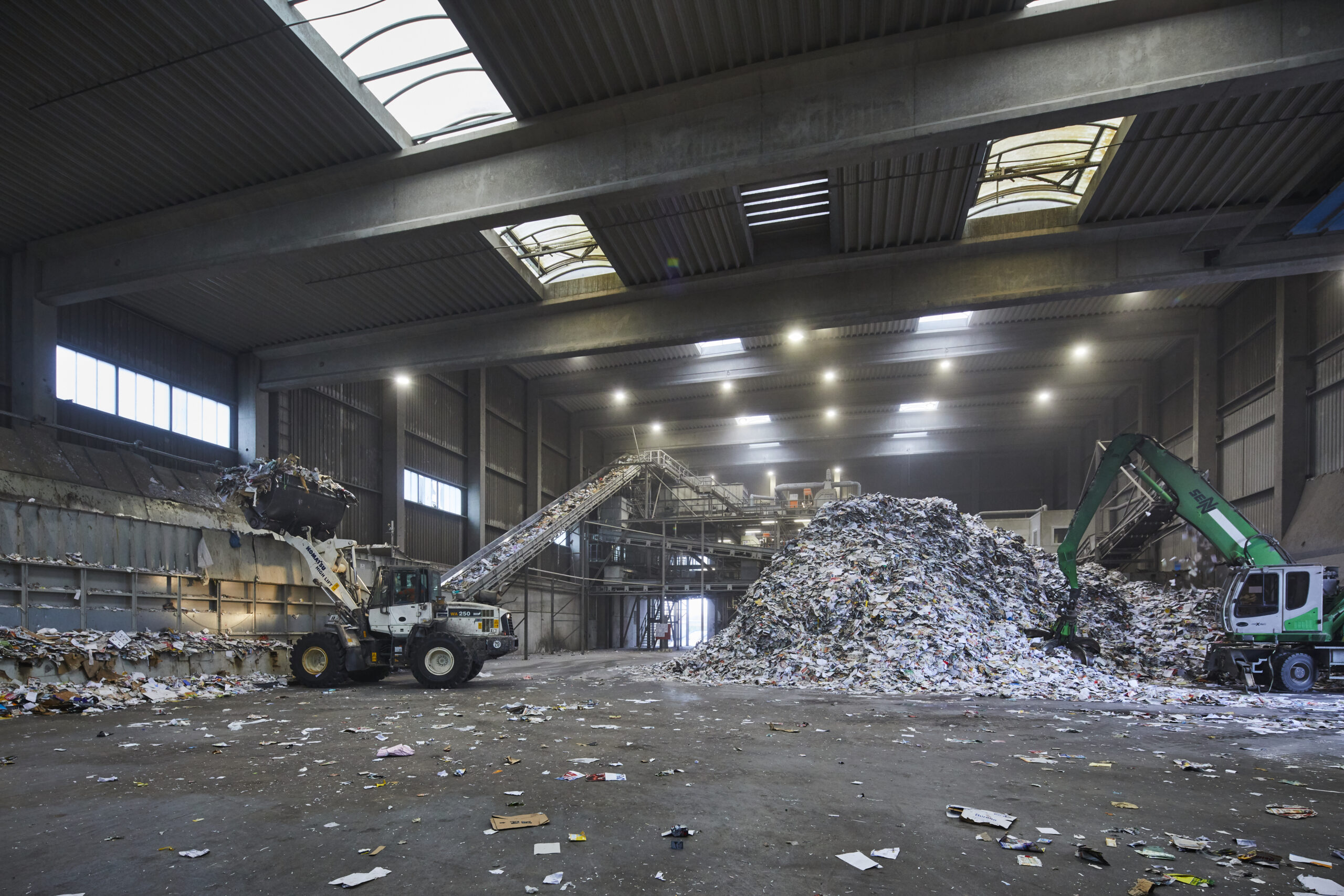
Right from the start, the Merkenich plant focused on reducing its maximum demand as this is the main factor that determines the size of its annual electricity bill. Each year it plans a one-off maximum demand and each year this figure is slightly lower than the year before. With maximum demand being reached relatively quickly in the cold months of January and February, there is effectively a virtual cap on consumption for the rest of the year. The plant’s operations are then run in such a way to avoid maximum demand during the remaining months of the year.
The plant’s baseload has also been able to be significantly reduced. The compressed air used in the facility was identified as being one of the main consumers of energy. As a result, the company has succeeded in clearly cutting its consumption of energy by deploying compressors with variable speed control.
Read about some other measures being taken by REMONDIS to save energy:
Image credits: image 1: Adobe Stock: dusanpetkovic1; images 2, 3: REMONDIS