Perfectly coordinated boiler cleaning work
One of the best ways to speed up shutdowns and get a plant up and running again in as short a time as possible is to deliver tailor-made services. As could be seen at the large-scale turnaround carried out at the waste-to-energy (WtE) plant in Essen-Karnap in 2018. By tailoring its services to meet its client’s precise needs, BUCHEN KraftwerkService was once again able to show just how flexible it is at planning and performing such projects, especially when it comes to cleaning boilers.
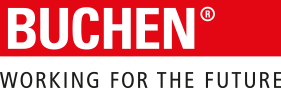
The plant is one of the largest of its kind
Over 740,000 tonnes of throughput material a year, 130 megajoules of district heat a second and around 50 megawatts of electricity – the waste-to-energy plant in Essen-Karnap is one of the largest of its kind in Germany. Three towns – 1 million local residents in all – benefit from the plant’s services. It is, therefore, very important for the region.
BUCHEN KraftwerkService provides services for conventional power stations, waste-to-energy plants and industrial boilers.
The operator of this facility, RWE Generation, has been working together with BUCHEN KraftwerkService for many years now to ensure the technology at the WtE plant runs smoothly. The focus of this work is on industrial cleaning tasks – both when the plant is online and offline. During the 2018 turnaround, which involved the whole of the plant being shut down for several weeks, BUCHEN KraftwerkService was in charge of all cleaning work needed for the four lines as well as the services involving the flue gas cleaning system.
Customised services required
It became clear while planning the work that a number of tailor-made services would be needed to complete the project – especially for cleaning the boilers. Two tasks, in particular, required special solutions: on the one hand, other tradespeople had to start carrying out their jobs in boilers 1 and 2 before the cleaning work had been completed owing to the tight schedule; on the other, an alternative had to be found for removing the dust so that the ID fan could also be overhauled.
Working at two levels
Detonative technology was used to perform the safety cleaning work in boilers 1 and 2 to speed up the whole process. This allowed large volumes of deposits to be dislodged from the walls and broken up while the boilers were still cooling down. The dislodged material was also able to be extracted while it was still hot. Two parallel extraction points and a special skip delivery system helped to further cut the time needed.
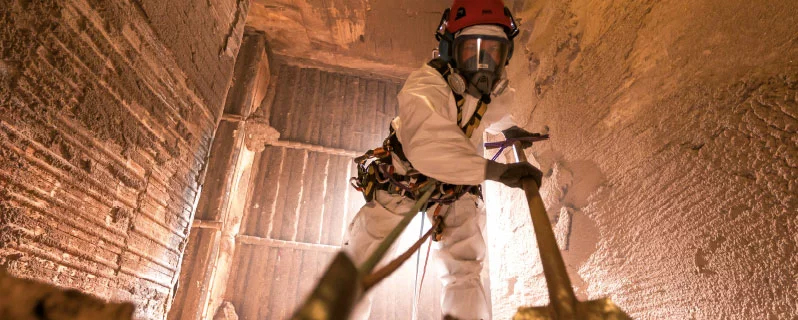
Over a dozen blasting specialists worked side by side every shift
A special work platform was set up for the subsequent sandblasting work to partition the area off. Pulled into the industrial furnace horizontally, it was then erected so that it had two separate work areas. Other specialists were able to carry out their work in the lower section where the boiler had already been cleaned. At the same time, BUCHEN KraftwerkService continued its own work cleaning the upper section of the boiler. The dislodged residue was collected on the upper platform, protecting those working below. With the different teams working like this for a week, several days were able to be shaved off the time needed for the shutdown.
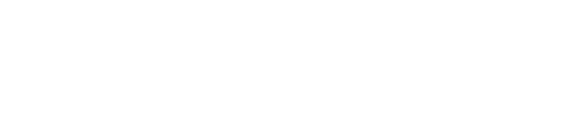
operatives worked around the clock in two shifts – and in both boilers at any one time.
Heavy-duty vacuum units in action
Heavy-duty vacuum units are a must for extracting dust from boilers. Which is why the plant’s own ID fans play an important role during shutdowns. This time, however, BUCHEN KraftwerkService took over this job itself to free up the WtE plant’s own fan. The company’s unusually large stock of specialist equipment had everything needed for this task so that four dust extraction units (output: up to 35,000m³ per hour) could be placed above and below the work platform.
Advice, cleaning services, remediation work and waste management – BUCHEN KraftwerkService’s portfolio covers all tasks and all plant sections.
All in all, BUCHEN KraftwerkService needed three weeks to carry out their tasks during this particular shutdown at the waste-to-energy plant. The teams worked around the clock in two shifts – with up to 60 operatives present in boilers 1 and 2 at any one time. Over a dozen blasting specialists worked side by side every shift – several hundred tonnes of blasting media was used during this short period. The project had been preceded by months of meticulous planning and preparation work and three weeks were also needed before and after to set up and dismantle the equipment. The bespoke solutions were drawn up during the planning phase and added to the schedule straight away to ensure everything went smoothly during the turnaround.
Image credits: image 1: © REMONDIS