Generally speaking though, high-performance EV lithium-ion batteries can withstand around 500 to 1,000 recharging cycles before they are finished – or at least they no longer have the power for drivers to race off at the lights. This does not mean, however, that the battery or the battery pack is useless and that it must be sent for recycling. Other options are available. Indeed, reusing the large batteries is an essential part of e-mobility for both the sector’s carbon footprint and its cost-effectiveness.
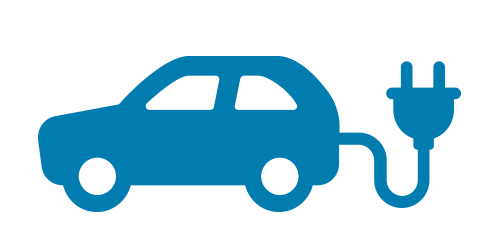
Generally speaking, high-performance EV lithium-ion batteries can withstand around 500 to 1,000 recharging cycles before they are finished – or at least they no longer have the power for drivers to race off at the lights.
Technical challenges
It is not so easy to answer the question whether a car battery can continue to be used. REMONDIS’ Swiss subsidiary Chiresa, which has owned a battery dismantling line since 2023, says that – as a rule of thumb – a battery must have a capacity of over 80% for it to be reused. The first step that the staff at BLC – The Battery Lifecycle Company take in the company’s two dismantling centres in Germany is to look at the housing and measure the temperature before even starting to remove the screws. If there are no signs of damage, then the BLC employees begin dismantling the battery and decide, step by step, whether they should stop after removing the peripheral components or continue working their way towards the actual battery elements.
If, at some stage of this process, the battery gets the thumbs down, then it undergoes a deep discharge. This permanently destroys the battery and it cannot be recharged again. Such batteries no longer pose a risk – were the battery not completed depleted, the up to 800 volts normally stored in it would make every step potentially lethal. The remaining dismantling steps can now be carried out under simple conditions. There are also fewer safety requirements for transporting these dismantled batteries by lorry compared to battery packs that are still functional.
“Recycling capacity will have to grow, albeit a few years later, as the number of EVs on the road increases.”
Lukas Brandl, Managing Director of BLC
Two particular challenges faced by dismantling firms are the rapid development of the battery market and selling the components. In many cases, they are not sure exactly how the battery has been built when they start their work. Matthias Illing, managing director of BLC, explained: “We have to know exactly how the battery has been put together and understand its cell chemistry. This is important to make the whole recycling process safe and effective. Our extensive experience is key here, as is our contact to our customers who have to compile the relevant documentation for their customers.”
The actual dismantling process is also a technical challenge as the employees have to have high voltage stage 3 certification. Which is why, for the most part, the company employs qualified electricians. BLC is also working on automating their dismantling and recycling processes. The first dismantling plant that it built, which is located in Rheda-Wiedenbrück, has the capacity to handle 5,000 batteries per year and most of the work there is carried out by hand. In contrast, its facility in Magdeburg already uses automation for certain processes, such as for the deep discharge, as it aims to achieve an annual capacity of 30,000 units. Lukas Brandl, managing director of BLC, stressed: “Recycling capacity will have to grow, albeit a few years later, as the number of EVs on the road increases. We’ll only be able to meet this demand with the help of automation.”
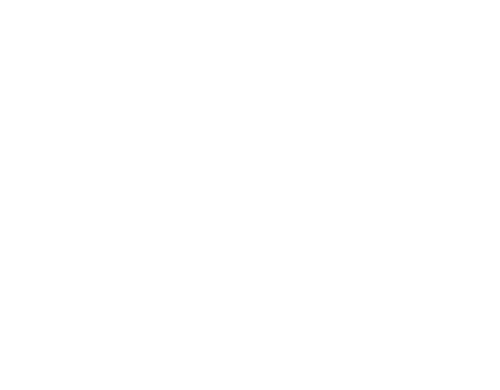
Rhenus and TSR found a joint venture
The Battery Lifecycle Company GmbH (BLC) was founded by Rhenus Automotive SE and TSR Automotive GmbH – both RETHMANN Group companies. In order to achieve its goal of offering a holistic range of battery recycling services along the whole of the supply chain, BLC will be taking on all stages of the process – from the initial checks, to the deep discharge, through to the repair and dismantling. It will primarily be handling lithium-ion batteries from the automobile industry.
TSR Automotive GmbH, a TSR Recycling subsidiary, owns a 65% share in the joint venture and will be running the new firm’s operations. Rhenus Automotive SE, a Rhenus Group subsidiary, owns the remaining 35%.
Alternative second uses
BLC, a joint venture between the recycling specialists TSR Automotive and Rhenus Automotive (both part of the RETHMANN Group), believes that an integrated approach is key. An approach that is reflected by the partnership itself: while TSR Automotive specialises in the reuse and recycling of vehicles, Rhenus Automotive acts as an assembly business for parts of the automobile industry. They have united the concept, ‘a business that put things together can take them apart again’, with the experience of dismantling used cars. BLC’s experts have identified four options for used EV batteries:
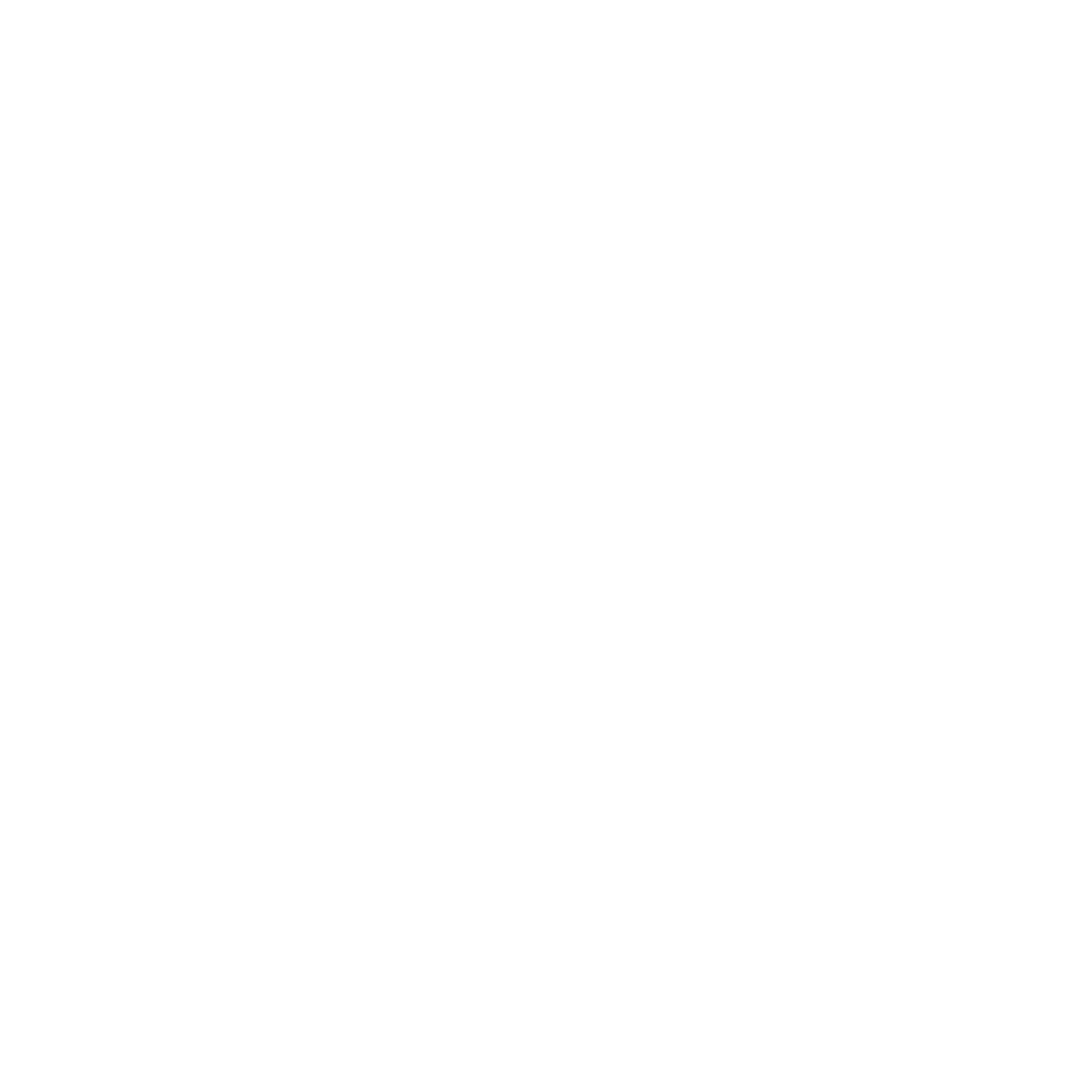
Repair/re-manufacturing:
The battery is partially dismantled so that the faulty battery elements can be replaced. The completely refurbished battery can then be installed in an EV again. The challenge here is having a sufficient number of identical batteries.
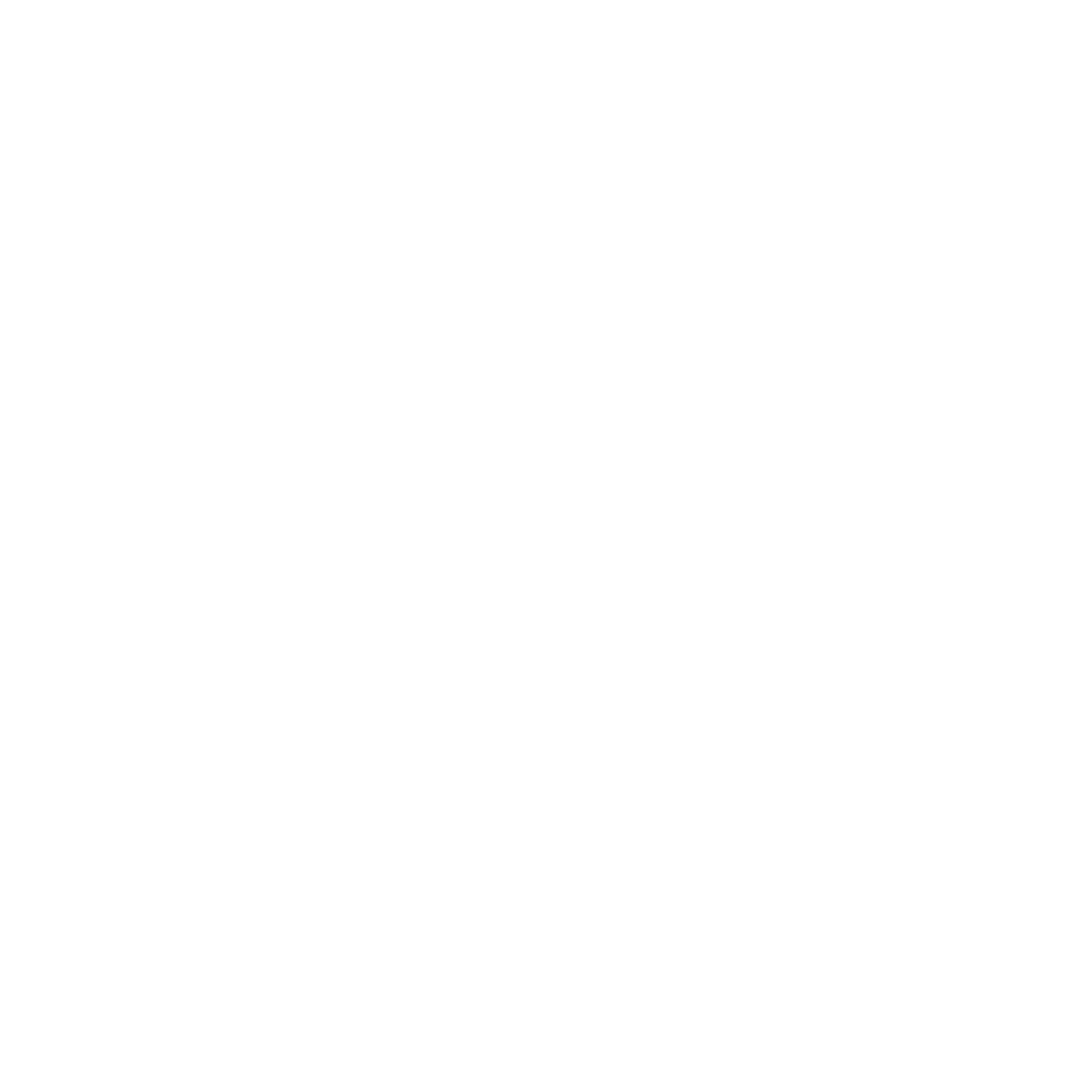
New application (second life):
The used EV battery is intact and is used for a new application as a complete unit. An excellent example of this are battery energy storage systems (BESS). Such systems have been used with solar panel systems and wind turbines for a long while but there is a clear trend now towards deploying second-hand units rather than new ones.
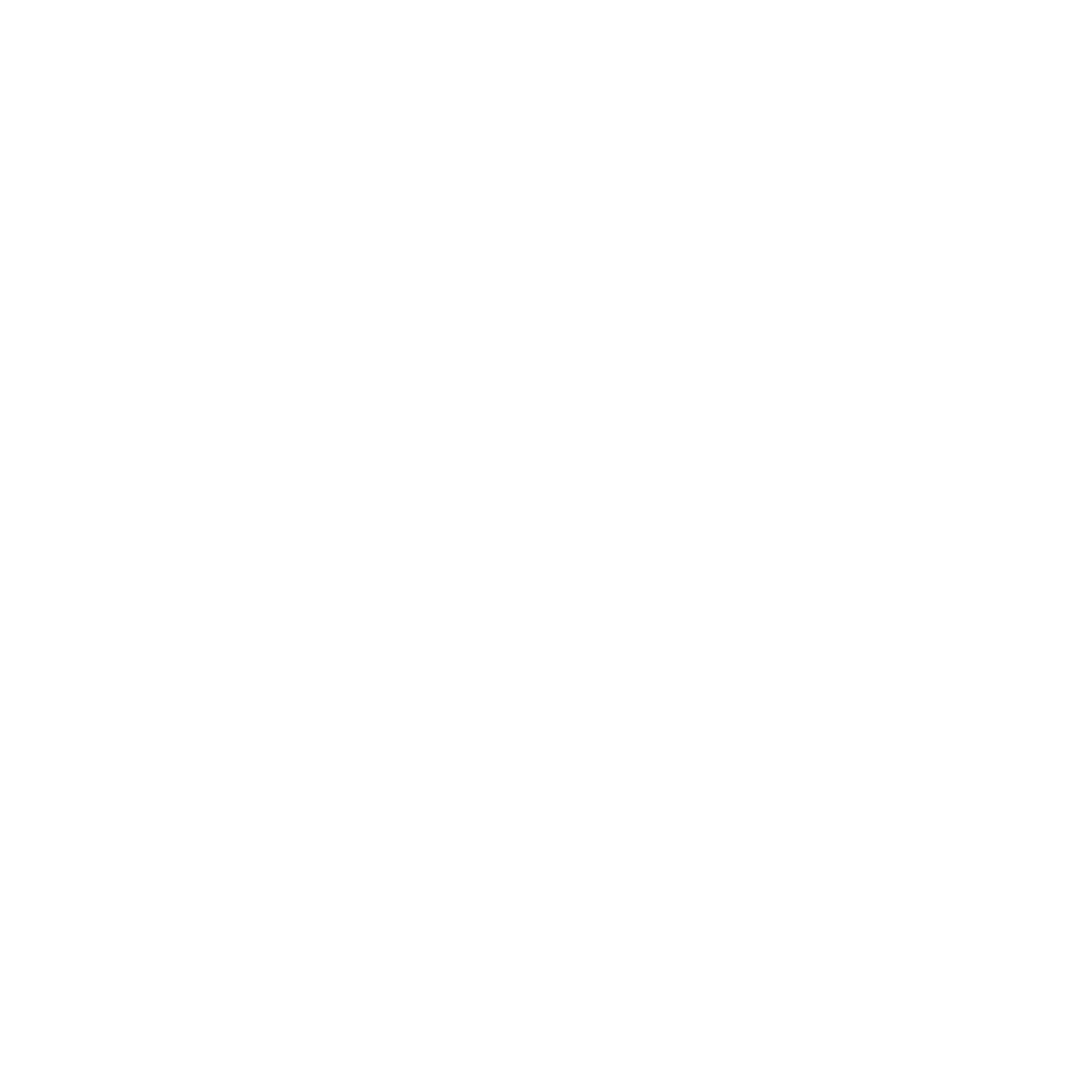
Recovery of spare parts:
The battery itself can no longer be used but its peripheral components (such as its control module and cable harness) can be recovered for reuse – in particular, as spare parts.
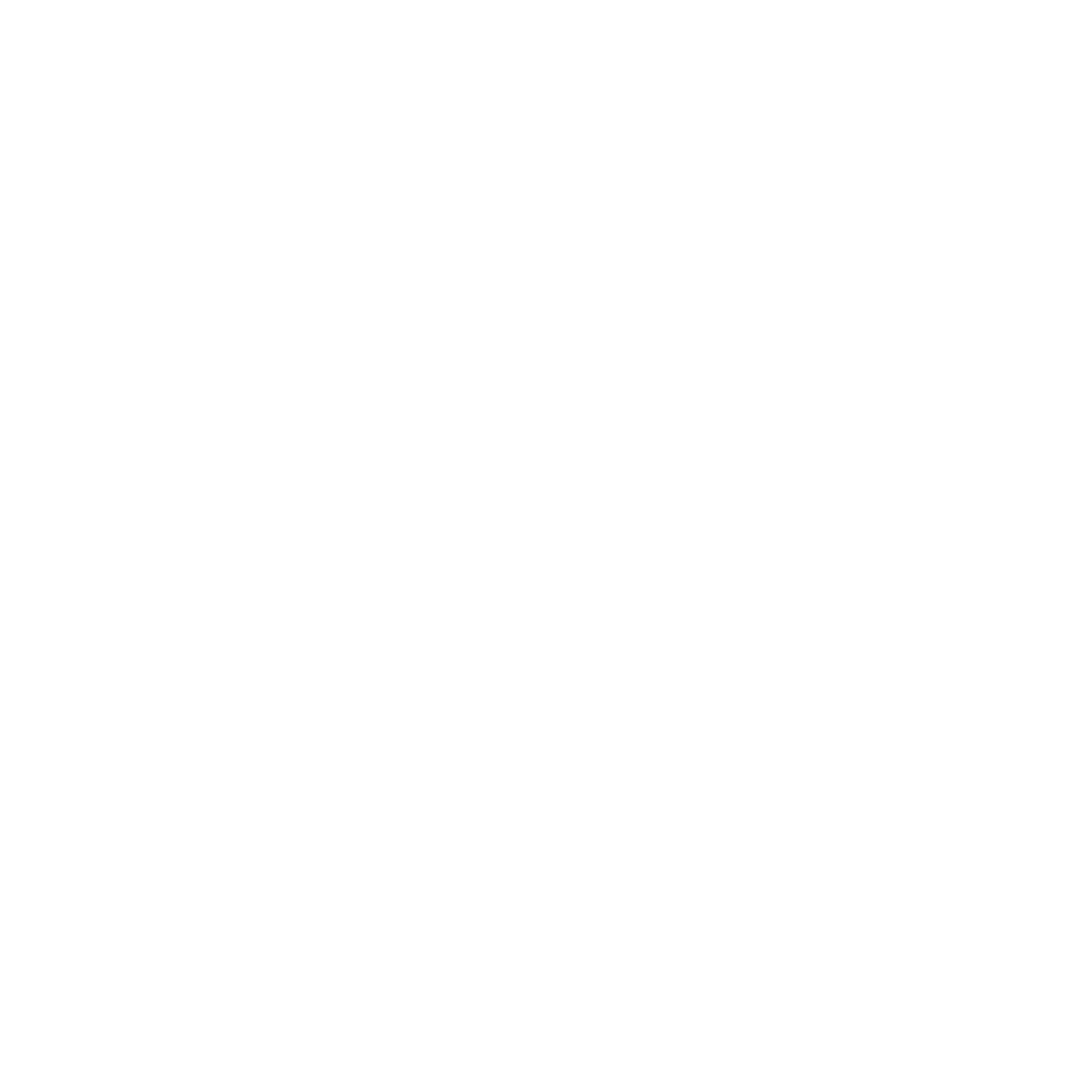
Recycling:
The battery is dismantled and its raw material contents are recovered for reuse, such as copper and aluminium.
At the moment, there are a large number of stand-alone solutions on the market. This automatically leads to more transport costs, for example if a business offering second life solutions discovers that the delivered battery is unsuitable for its needs and has to send it on. On the other hand, it is almost impossible to avoid batteries being incorrectly allocated:
which company specialising in recovering spare parts is interested in repairing a battery that is effectively intact? It is precisely for these reasons that BLC is working on an integrated approach, driving forward automation, gathering experience and already thinking about setting up further dismantling centres.
You can find more articles on batteries here:
Image credits: image 1, 2: Shutterstock: IM Imagery