And yet just a tiny proportion of the plastic waste generated around the world is recycled. What’s the reason for this? What could be done better? And what might the future look like for the chemical recycling of plastic.
For decades now, global production of plastics has been spiralling upwards. 367 million tonnes of plastic were manufactured around the world in 2020. This is almost four times the amount of plastic produced at the beginning of the 1990s. Experts have forecast that this dynamic market growth will continue into the future – driven on by new uses for this versatile material and the increasing demand coming from emerging economies.
A large share of the plastic produced today is used to manufacture packaging. The share of the packaging sector in Europe, for example, lies at a good 40%. Packaging, however, is used for a particularly short period of time. It is discarded as waste much faster than other products – moving quickly into the segment where handling plastic becomes a challenge.
World plastics production p. a. (in mt)
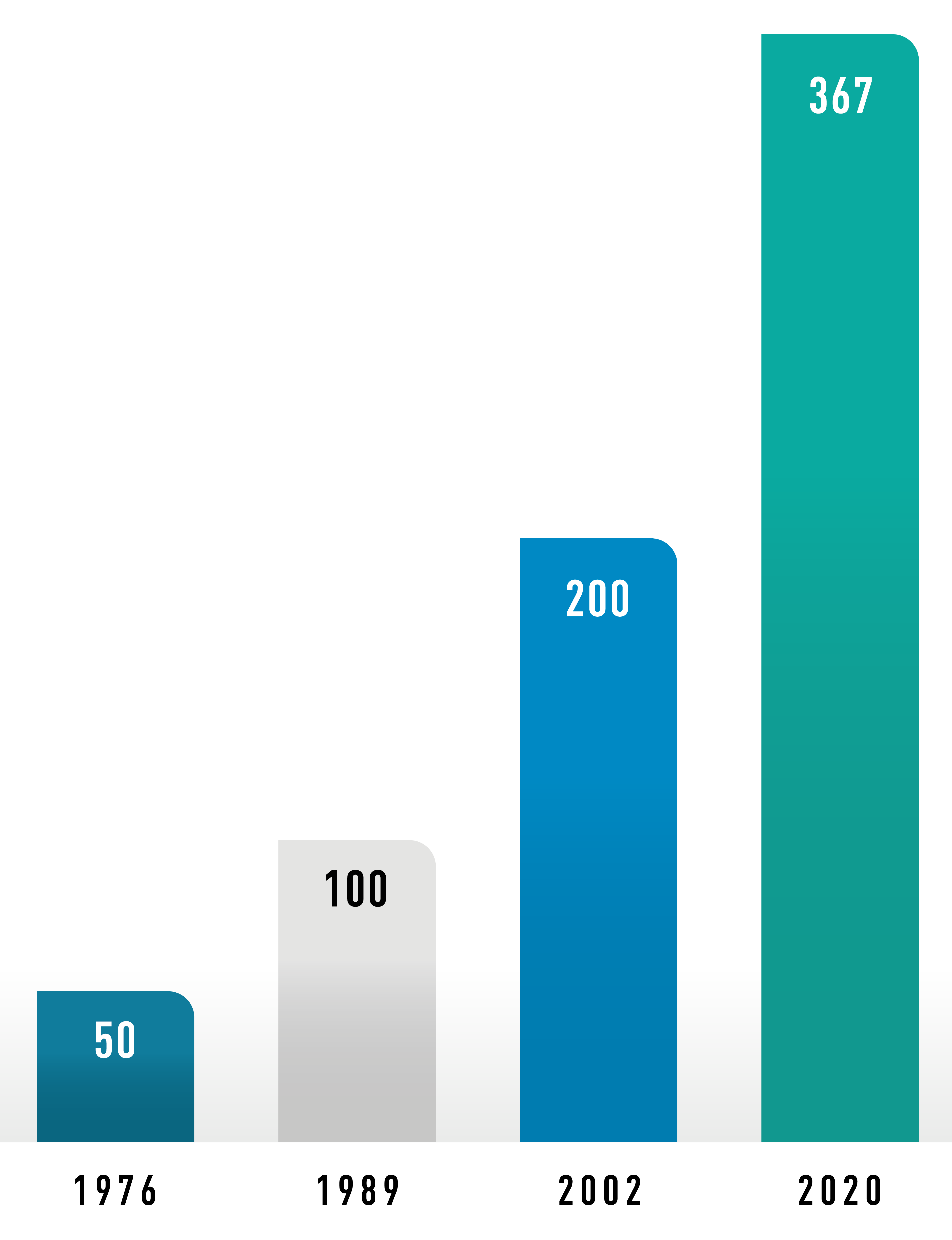
Sources: The Compelling Facts About Plastics, Plastics Europe, 2008 | Plastics – the Facts 2021, Plastics Europe, 2021
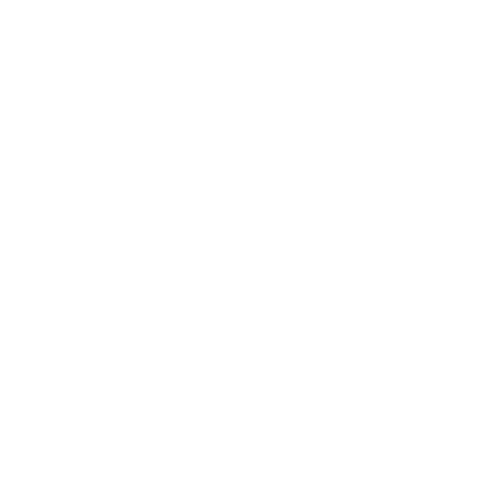
Just 20% of plastic waste generated around the world is recycled
Conversio, a market research company, took a detailed look into what happens to plastic after it is no longer needed. The findings of their analysis of global plastics flow in 2018 are sobering. Almost one-third of global plastic waste is not collected, which means it is not sent for professional treatment. Just under one third is collected but is sent to managed landfills. A mere 40% of old plastics, therefore, is collected and processed, with half of these materials being sent on for recycling and half for energy recovery. If the share sent for materials recycling is isolated from the rest, then a mere 20% of global plastic waste is actually recycled for reuse.
As can be expected, the situation in Europe is more positive. Having said that, though, large volumes of discarded plastics are not being sent for recycling here either. In 2020, around 35% of post-consumer plastic waste was recycled for reuse in the European Union plus Norway, the UK and Switzerland. The remaining 65% was sent either for energy recovery or to landfill – two routes that mean that any possible reusable materials are lost to us forever.
Route taken by global plastic waste (2018)
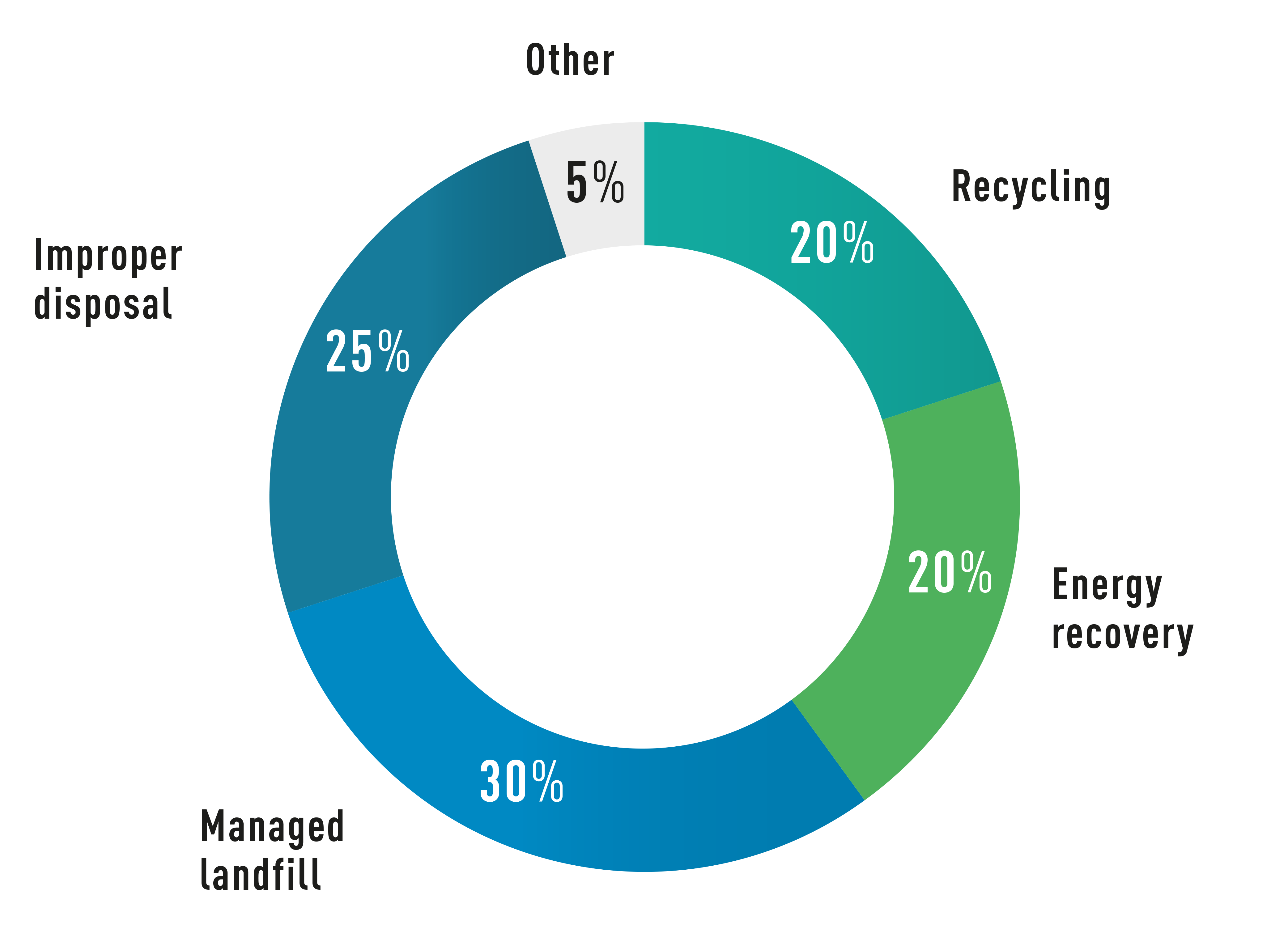
Source: Global Plastics Flow 2018, CONVERSIO Market & Strategy, 2020
European – and, in particular, global – waste plastic streams show that there is still much room for improvement despite the successes achieved in plastics recycling to date. To be able to tap into this potential and develop a circular economy, storage, collection and recycling structures need to be set up in those areas where they are lacking or partially lacking. If the recyclable materials contained in the plastics are to be systematically recovered for reuse, then landfilling must be phased out at a faster rate. At the same time, plastic materials being sent for energy recovery should, wherever possible, be diverted to recycling facilities.
Route taken by collected post-consumer plastic waste (EU + UK, Norway, Switzerland, 2020)
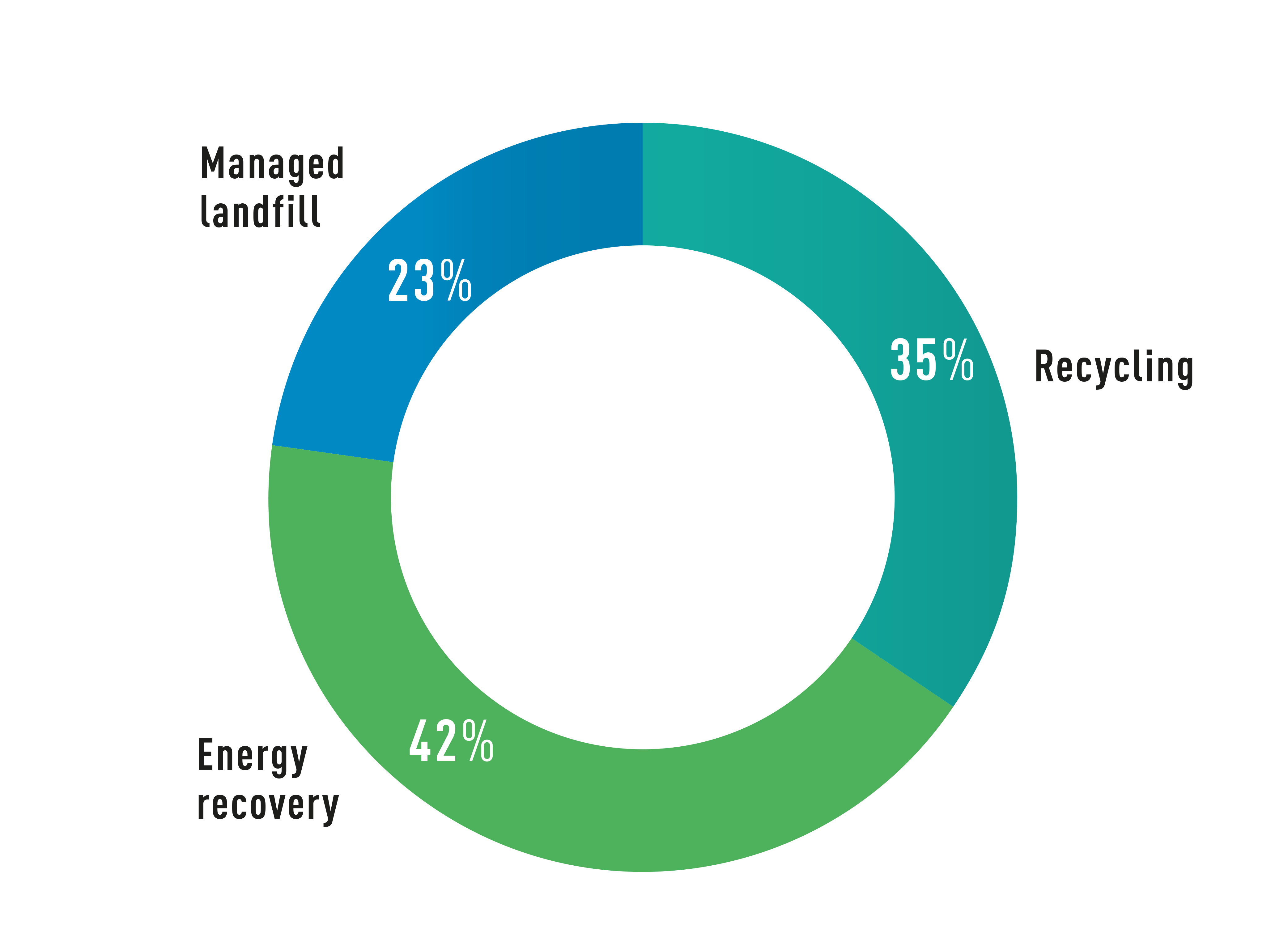
Source: Plastics – the Facts 2021, Plastics Europe, 2021
Tried & tested: mechanical recycling
There are big differences within Europe itself. In Germany, for example, more than 99% of plastic waste was processed in 2019 with around 47% of this material being sent for recycling and almost 53% for energy recovery. It is not only the goals of the individual European countries that impact on recycling rates but their rules and regulations as well, such as the German Packaging Law. Alongside this, there are the efforts being made to reduce the volumes of plastic waste being generated in the first place, especially at industrial and commercial businesses.
If plastics are recycled today, then they undergo mechanical recycling processes. These systems have been tried and tested and are well established on the market. Being one of the pioneers in this sector, REMONDIS has been recycling plastics for over 50 years – using certified production methods to produce a whole range of recycled plastics, so-called recyclate, on an industrial scale. During this multi-stage procedure, the plastics are first separated strictly according to type before undergoing a combination of mechanical-physical processes including sizing, washing, contaminant removal and extrusion.
Mechanical recycling rates of plastic waste
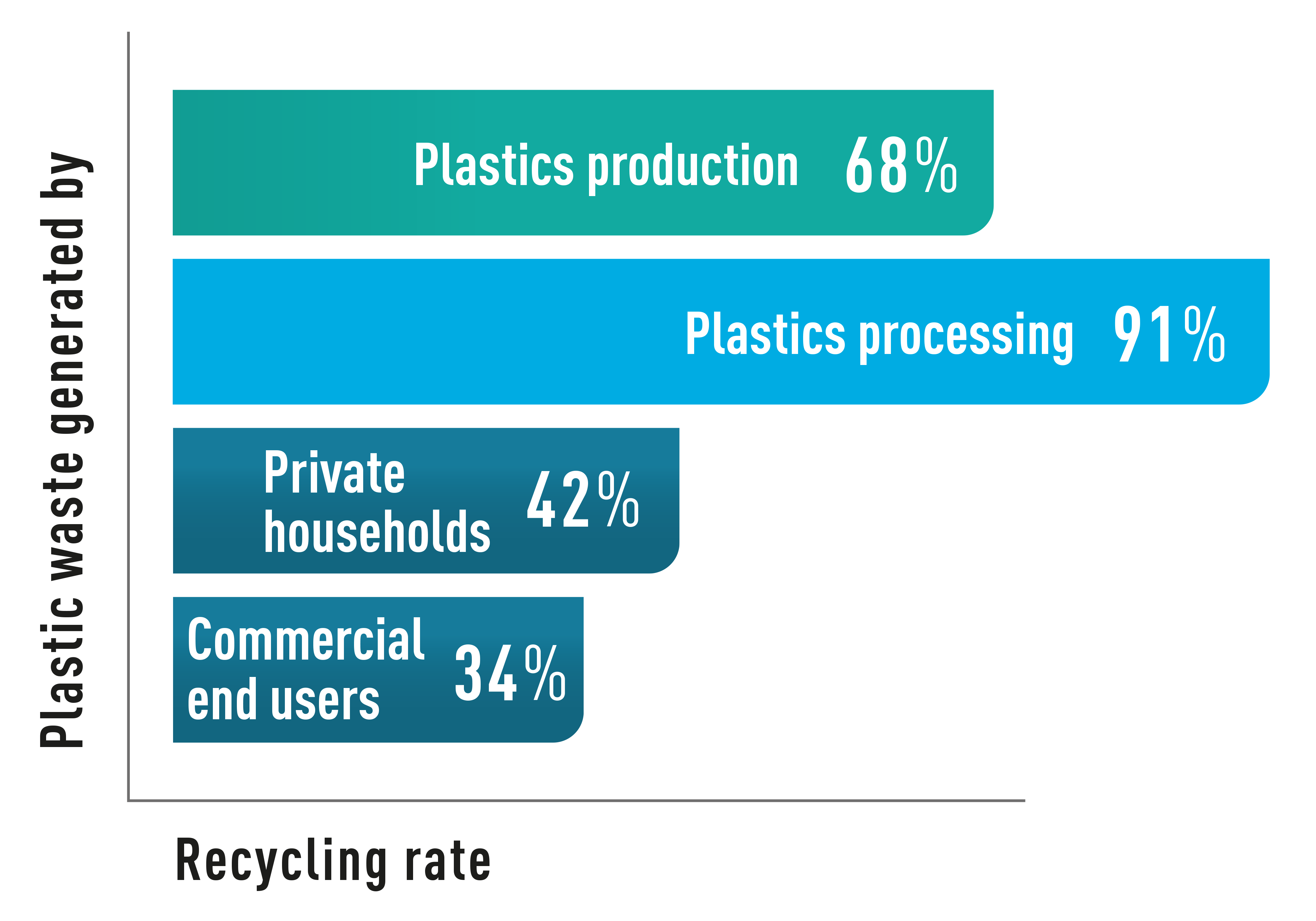
Source: Statusbericht der deutschen Kreislaufwirtschaft 2020, 2020
At the end of the process, the company has produced pellets, compounds, agglomerates and ground products with defined uniform properties that have a consistently high quality and can be used to substitute virgin plastics. There is a steady demand for these recycled products. Around 12% of the raw materials used by all segments of the plastics processing industry in Germany is recyclate. This figure lies at 9% in the packaging sector.
The better the input material has been separated before it reaches the recycling facilities, the higher the quality of the recyclate produced by the mechanical processes – and, consequently, the more applications it can be used for. A recycling rate of over 90% is possible with the relatively homogenous volumes of waste generated by plastics processing businesses and plastics producers. In contrast, the recycling rates of the mixed fractions from private households and commercial end users lie below 50%. What is left over is mixed plastics, sorting residue and fractions of plastics that are unable to be recycled either from a technical and/or business point of view. Further developments in sorting and processing technology will further reduce the volumes of non-recyclable materials. Investments are already being made in such technology across the EU.
The ideal way to grow plastics recycling rates is to have a combination of high performance mechanical recycling and chemical recycling, a technology that is currently being developed.
A complementary system: chemical recycling
Besides mechanical recycling, the spotlight is also being gradually turned on chemical recycling technologies. Chemical recycling transforms plastic waste into chemicals that can then be used as raw materials in chemical processes. A variety of technical procedures can be deployed to bring about such a transformation, such as pyrolysis. By adjusting pressure and temperature, the plastics are broken down into a gas and then condensed into pyrolysis oil. Plastics manufacturers could replace virgin fossil raw materials with this oil and use it to produce new plastics. One of the key advantages of chemical recycling is that the pyrolysis plants can handle mixed fractions of plastic waste. The chemical recycling route can, therefore, be used for materials that are less suitable or indeed unsuitable for mechanical recycling.
The input material sent for chemical recycling also determines the quality of the recycled products. At the moment, focus is being put on mixed plastic waste, around three-quarters of which comprises polyolefins, i.e. polypropylene or polyethylene. The remaining 25% can be made up of other types of plastics, such as PET or polystyrene, and contain foreign particles, e.g. particles of metal and paper. As far as the mixtures of material are concerned, however, it should be noted here that the chemical recycling of plastics is still in its infancy. Looking ahead into the future, more complex mixtures of plastic waste will be able to be treated as technological advances are made. Strategic partnerships between the recycling sector, the chemicals industry and providers of such technology will be one of the main drivers of such progress.
As chemical recycling uses mixed fractions, this system has, theoretically, great potential. If all of the post-consumer plastic waste in Europe that is currently being sent for energy recovery were to be chemically recycled, then – in purely mathematical terms – more than 12 million tonnes could be sent for higher quality recycling – assuming that these materials are not suitable for mechanical recycling. Additional options would be generated by further phasing out landfills and diverting these materials to recycling facilities instead.
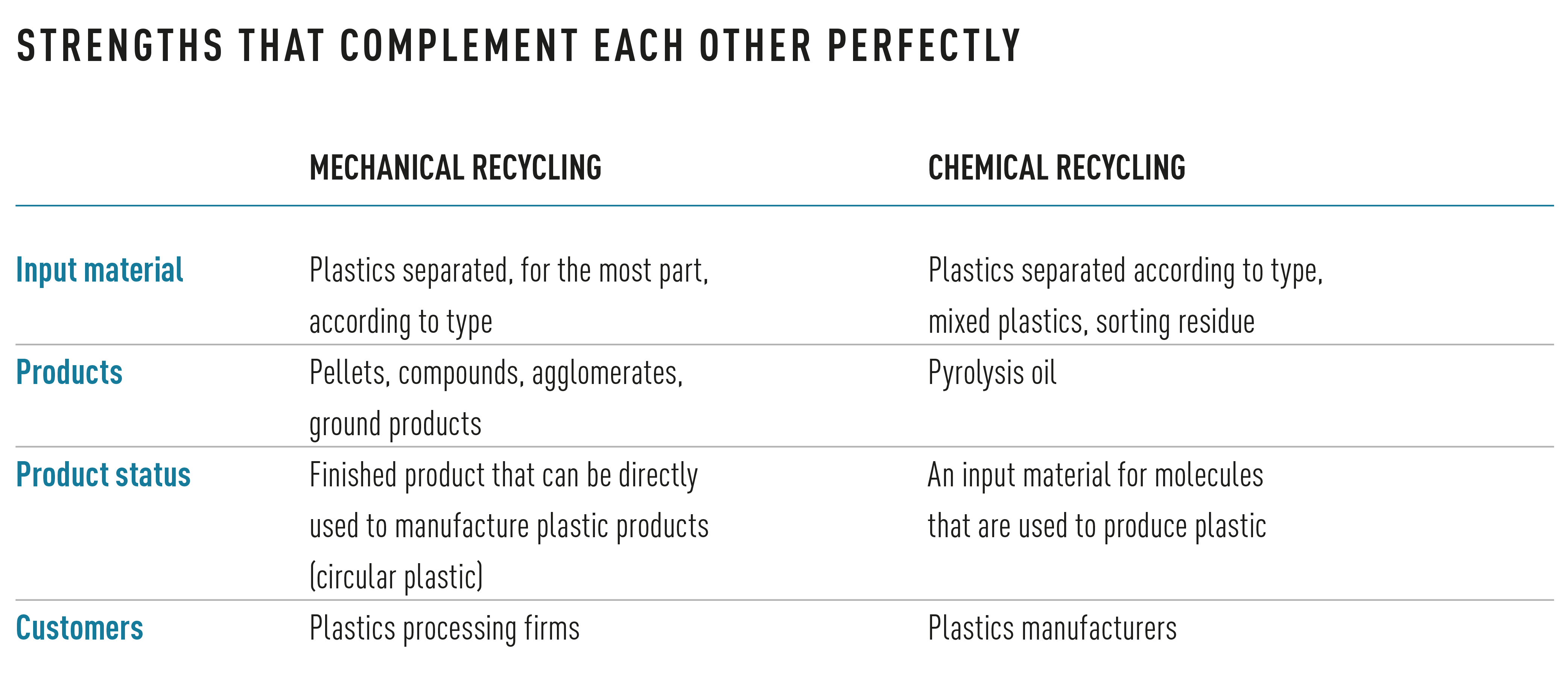
No matter whether it be mechanical or chemical recycling: there is great interest in plastic-based recycled raw materials. Besides the positive impact this has on tackling climate change and conserving natural resources, there is also a growing need to ensure there is a secure supply of raw materials. At the end of the day, producing petroleum- based plastic is highly dependent on imports and developments on the global market. The latest developments have highlighted just how uncertain this environment can be. Supply chain disruptions led to 35% of the VCI member companies [German Chemical Industry Association] scaling back their production activities in Germany in 2021; a further 10% were forced to temporarily shut down their production altogether. A situation that has been further aggravated by the war in Ukraine and its ramifications.
The European Union is also providing momentum in this area, stating in its Green Deal that 55% of all plastic waste should be sent for recycling by 2030. What’s more, it is planning to set minimum recycled content requirements for new plastic products. As far as the packaging sector is concerned, the amount of plastic recyclate currently being used in new products could – purely from point of view of technology and with a few moderate limitations to the properties – already be more than doubled today and achieve the targets set.
One factor holding back chemical recycling is that this process has not been officially recognised as a form of materials recycling. The Ministry for the Environment in Germany considers chemical recycling activities to be raw material recycling, which means it falls under the definition of recycling as set out in the German Circular Economy Law [KrWG]. In contrast, the German Packaging Act [VerpackG] states that materials recycling exists when the recycled material substitutes the same virgin material. Pyrolysis oil does not meet this requirement. According to the Ministry, therefore, the amount of chemically recycled materials may not be added to the recycling rates achieved by the packaging sector.
As to how far chemical recycling actually makes sense will also be determined by how much the pyrolysis oil will be able to be reused. Industry can use the oil as a feedstock in cracking plants and break it down into molecules that can then be used as a raw material for new products. It has not yet really been resolved, however, which products these might be. Relevant industrial feasibility studies and pilot projects are currently being carried out but – just like chemical recycling itself – they are still in their infancy. Furthermore, it must also be considered that pyrolysis oil starts at an early stage of the production chain. Unlike recyclate, extensive steps are required to create a polymer. What’s more, the amount of elements in the pyrolysis oil that can actually be used to produce plastics is low.
Last but by no means least, it will depend on whether it makes long-term financial sense to invest in chemical recycling plants and this, in turn, depends on future market developments. What will be key here will be whether mechanical and chemical recycling systems can be established as complementary processes, with each being able to make the very most of their advantages.
What must not happen is that they end up competing for input materials. Material fractions that have been separated according to type must continue to be sent for mechanical recycling as the recyclate can be used in a later processing stage of the plastics production chain, thus reducing the energy consumption of the upstream production activities.
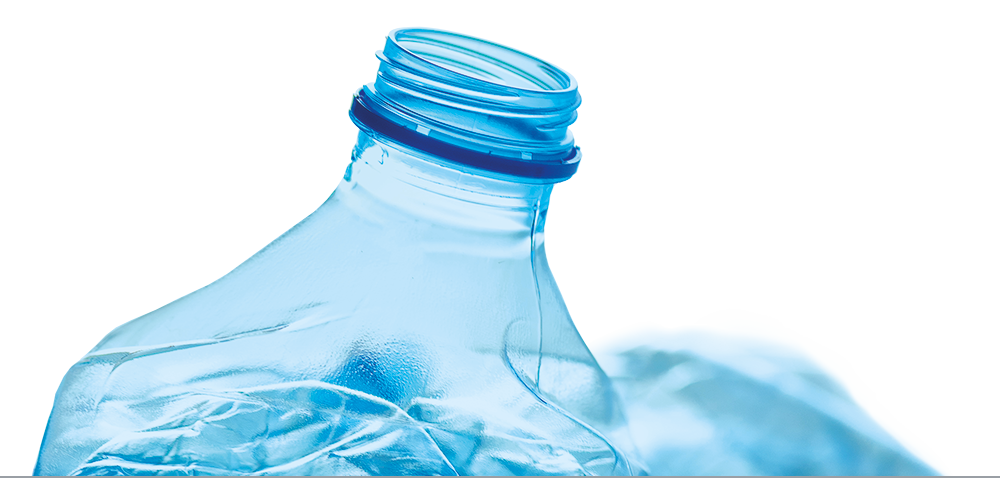
When it comes to plastics recycling, REMONDIS remains open to future findings and is helping to drive both systems forward. It continues, as always, to focus on carrying out mechanical recycling on a grand scale. Alongside these activities, REMONDIS has also set up partnerships with industrial businesses to further develop the various approaches to chemical recycling. The reason behind this is simple: in order to achieve the ambitious sustainability goals and the greatest possible levels of supply security, it is essential to develop every possible recycling activity that is technically and economically viable.
Image credits: image 1, 2, 3: Adobe Stock: Bits and Splits