Major advantages for customers
The maintenance sector is on the verge of undergoing a fundamental paradigm shift: digitisation and high-tech are paving the way for predictive applications. XERVON Instandhaltung, XERVON’s maintenance specialists, are embracing these innovative opportunities and developing practical options that will offer their customers some key advantages, especially in the areas of efficiency and cost effectiveness.
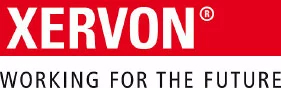
Early warning systems
When it comes to maintaining rotating equipment, such as turbines, pumps and compressors, it is condition monitoring that is the measure of all things nowadays. This type of maintenance system takes online and offline measurements to gather information about a machine’s condition and sets certain limit values. Deviations can be spotted immediately, enabling suitable countermeasures to be taken in good time.
XERVON is constantly screening the market to identify technologies that will be of use to its customers and managing trends with its trend radar.
New opportunities are opening up here, too. Technological progress and recent developments, such as ‘machine learning’ and ‘big data’, are making it possible for a level of maintenance to be achieved that gives us an idea of what things will be like in the future. At the centre of all of this are the predictive maintenance systems. They act as an early warning system, predicting what will go wrong in the future and enabling faults to be prevented before they actually occur.
A key innovation of Industry 4.0
The field of predictive maintenance may still only be in its infancy but it is already being heralded as one of the key innovations of Industry 4.0. Which also explains why XERVON has been focusing its attention on growing its own application-related know-how in this area for a while now. Its goal here is to add predictive maintenance solutions to its portfolio of services that will open up some interesting prospects for its customers. These systems will offer a whole range of advantages – especially when it comes to increasing plant availability. According to a McKinsey study, around half of all machine and plant downtime will be able to be prevented with predictive maintenance.
By growing its expertise, XERVON Instandhaltung has become an adept partner for IoT applications as well.
The core idea behind XERVON Instandhaltung’s projects is to use machine learning to make plants and facilities smarter. The data that the sensors collect about the condition of the machinery is added to other information – for example data about the ambient temperature or humidity. All this data is then analysed using state-of-the-art technology that enables anomalous patterns to be picked up. This in turn makes it possible to predict problems that may occur in the future.
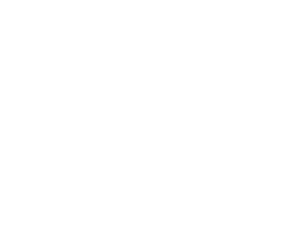
The core idea behind XERVON Instandhaltung’s projects is to use machine learning to make plants and facilities smarter.
An award from the itelligence of Things initiative
XERVON is combining its extensive maintenance expertise with its IT and digitisation know-how in order to be able to offer its customers practical solutions in this field. At the heart of all this data is an IoT platform. Its task is to merge the information gathered from the different types of technologies and platforms and connect it to database inventories.
Cutting costs, optimising operating conditions, minimising downtime: predictive maintenance offers customers a whole host of advantages.
It was possible to see just how far XERVON has already progressed in this area during the itelligence of Things competition organised by SAP’s consultancy business, itelligence. Facing competition from a total of 25 companies, XERVON’s concept was awarded one of the main prizes. Work is already being put into implementing this concept, for example on the pumps and motors used in cooling towers.
Machines can be run more efficiently
Predictive maintenance allows these important components of the cooling water supply system to be controlled at the best possible operating point and to determine exactly when they should be switched on and off. What’s more, the operating hours can be spread intelligently across the different pumps. This makes the whole business far more efficient, reduces electricity consumption and cuts costs. Furthermore, there is less wear and tear which means greater plant availability and fewer maintenance costs.
Putting the system to the test
XERVON recently set up its own test stand at the ChemTech Hackathon in Cologne in order to bring its work in this area a few steps closer to being put into practice as well as to generate some new ideas. During the event, specialists from the chemicals industry and the world of IT looked at the innovations that might reconcile the challenges faced by both areas. It was made clear here that XERVON’s model could indeed be realised, taking it one step closer towards making it to market.
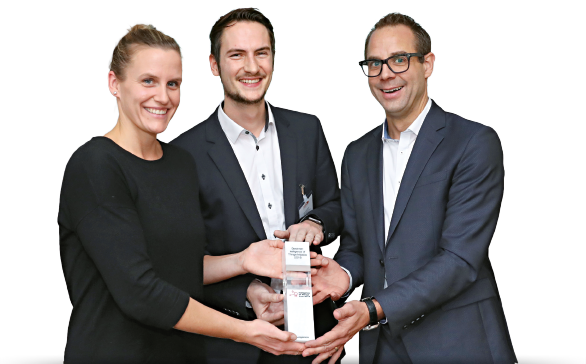
The predictive maintenance project submitted by XERVON to the itelligence of Things competition was awarded one of the main prizes. Mark Albrecht, Vice President Global Head of Innovation at itelligence AG, presented the prize to Tim Grylewicz, Head of Digitisation at XERVON Instandhaltung, and Alexa Kopp, Head of Project Management at XERVON Instandhaltung (from right to left)
Image credits: image 1: Adobe Stock: AndSus; image 2: © REMONDIS