Replacement work needed every three to six years
The most notable use of the electromembrane process around the world is the electrolysis of sodium chloride to produce chlorine. If the performance levels of the plants are to be maintained, however, then the membranes have to be replaced regularly – generally every three to six years depending on the current density deployed. XERVON IPS has developed a package of highly specialised services for this particular field of work.
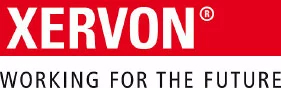
Environmentally friendly technology
Chlorine is one of the most important basic chemicals. Indeed this substance plays a significant role – either directly or indirectly – in up to 70% of all chemical products. As this chemical is so important, many companies choose to produce the chlorine they need themselves using electrolysis. The majority of modern chlor-alkali electrolysis plants use the membrane process. This environmentally friendly technology delivers a particularly pure end product. The main disadvantage of this system, however, is that the membranes can only be used for a limited period of time as foreign particles tend to stick to them and disrupt the process. Replacing these delicate membranes is both complex and time-consuming. At the end of the day, an electrolysis plant is made up of 162 elements, all of which must be dismantled so that the membranes inside the system can be replaced.
Specialisation means greater precision & faster work
Around ten years ago, XERVON IPS, a company owned by XERVON Instandhaltung, developed a special package of services to speed up this complex task of replacing membranes and to save its customers both time and money. One of the biggest strengths of these services – which are being continuously optimised and fine-tuned – is that they are so highly specialised.
The operatives carrying out the work, for example, are experienced industrial mechanics who have taken part in a specialist training course that looks in detail at the process of replacing membranes. Furthermore, they receive additional training ahead of each individual project to learn all about the specific features of the customer’s facility.
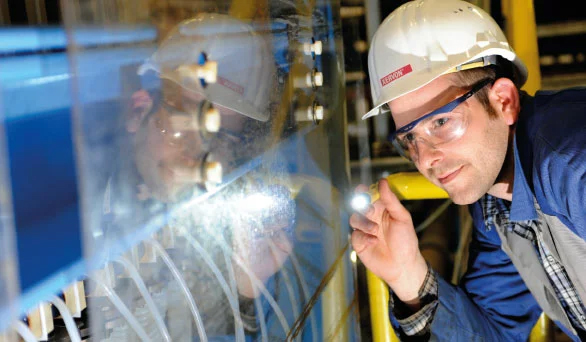
No room for error
Thanks to these measures, the staff have become true experts in their field enabling them to deliver their services faster and with greater precision. These are two major advantages as there is no room for error when it comes to replacing the membranes. Not when they are dismantling the individual elements and not when they are installing the new membranes. Even the smallest of kinks or the slightest damage will affect the way the membrane works. If tiny microparticles get left behind on the anodes or cathodes, then they may cause irreparable damage to the new membrane so that the whole replacement procedure has to be repeated.
Being experienced maintenance experts, XERVON IPS specialised in replacing membranes in electrolysis plants – or remembraning as it is also known – a long while ago.
Besides dismantling the units and replacing the membranes, XERVON IPS’ portfolio also includes carrying out pressure tests on the individual elements, checking the plant parts for signs of wear and tear, examining the coating and, where necessary, performing the recoating work. Once the plant is up and running again, the operatives monitor the operations via a computer, carry out a plausibility check and document all the work they have done. XERVON IPS has added a new service this year: processing the sets of screws used in the plant. While to some this work may initially seem to be of little consequence, it does in fact create some major cost advantages for the customers. With each individual electrolysis element needing 74 screws, the whole plant contains a total of almost 12,000 screws. Thanks to this new service, these can be reused after they have been processed, significantly reducing the overall costs.
Helping to cut energy consumption
XERVON IPS’ membrane replacement services are in high demand. Replacing the membranes not only gives the customers peace of mind that their plants will continue to function smoothly. It also enables them to upgrade their systems as the old membranes can be replaced with the new generation of membrane that delivers a higher yield without having to increase energy input. The maintenance and installation work, therefore, not only makes sure the plants continue to deliver a top performance, it also helps reduce energy consumption.
Image credits: image 1: Fotolia: Minerva Studio; image 2: REMONDIS