It is a challenging task to ensure that the highest levels of health and safety are in place in a working environment. And this is especially true when it comes to industrial services. At the end of the day, the teams of operatives work in unfamiliar industrial plants, in sensitive environments, high above the ground and in confined spaces – and carry out tasks that are not without risk. BUCHEN and XERVON make the most of all the avenues available to them to make sure that they achieve the best results in such conditions. Take a look below to find out more about their work in the field and their different initiatives – the two of which fit together perfectly.
Safety awards are something special. Companies looking to win one of the highly coveted safety prizes awarded by refineries, chemicals firms and other industrial businesses must first prove that they have outstanding safety measures in place. And they must often do this over long periods of time and take part in multi-stage evaluation processes – processes that include unannounced safety audits, involve stringent criteria and expect excellent accident records. This doesn’t seem to be a problem for either BUCHEN or XERVON. These two industrial service providers – united by REMONDIS Maintenance & Services – are presented with well-known awards by their customers almost on a regular basis.
These prizes are a mark of recognition that not only attests to the fact that their safety levels go beyond the norm but also confirms the success and positive impact of their in-house safety culture. Its special feature: health and safety at work is promoted and driven forward by each and every employee. By their QHSE departments (quality, health, safety and environment), by all of the other departments and by all of their operational units. “Health and safety at work is an integral element of our corporate responsibility and a sign of quality as well. It is a joint task that everyone must support wherever there is the potential to further improve standards,” commented Adrian Wortmann, head of the central QHSE & sustainability department. The following eight examples demonstrate how this is reflected in their everyday working life and what precisely can be done to create safe working conditions.
“Health and safety at work is an integral element of our corporate responsibility and a sign of quality as well.”
Adrian Wortmann, Head of the Central QHSE & Sustainability Department
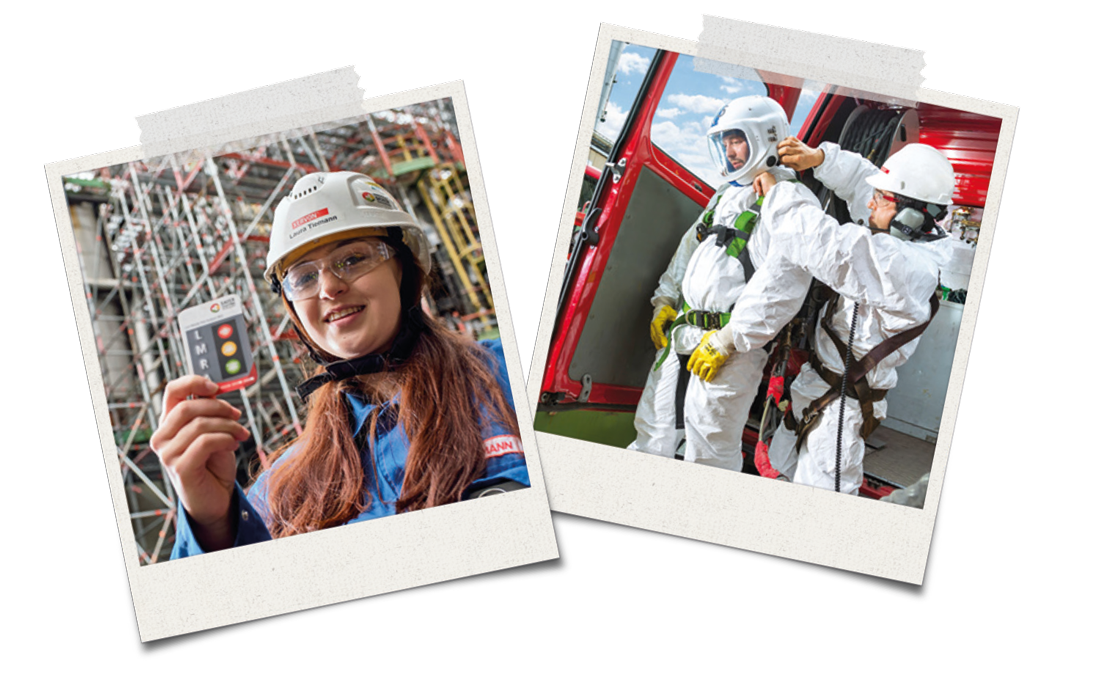
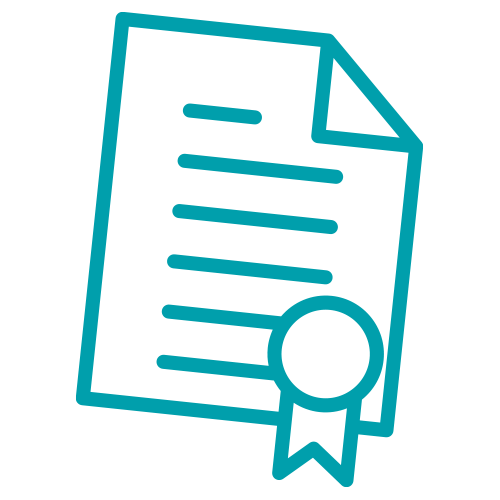
1. Certificates & accreditations. The basis for everything.
The company has set up an integrated management system in line with international standards and it is this system that forms the basis for safety and other aspects of the business across the group. It covers all operational processes as well as all related control and supporting processes. Statutory regulations are taken into account as are technical standards, customer requirements and internal guidelines. The variety of pertinent health and safety accreditations range from DIN ISO 45001 to the industry-specific Safety Certificate Contractors (SCC) certification.
All in all, REMONDIS Maintenance & Services, BUCHEN and XERVON have been awarded certification in line with more than ten norms and rulebooks. These are supplemented by the special certificates and permits that have been awarded to the companies’ operatives, such as those connected to the German Ordinance on Industrial Health and Safety [BetrSichV]. These many accreditations are not only of great importance within the company. They are also proof that the implemented QHSE measures have been audited by external specialists – providing a reliable set of criteria for others to assess the levels of quality used to manage health and safety. An aspect that is of importance to customers and employees alike.
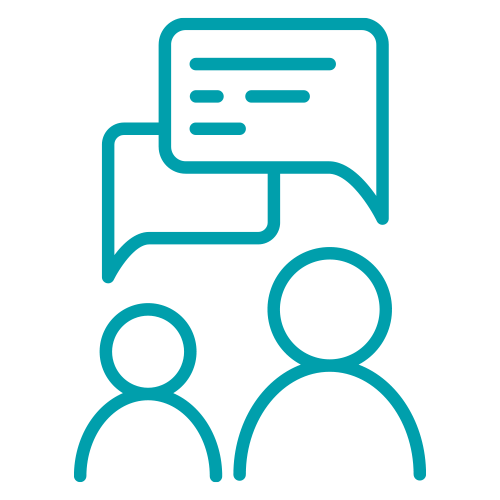
2. Training. Those all-important skills.
The more employees know about health and safety, the safer they are when they carry out their tasks. Well aware of this, the group has set up its own training system (a combination of in-person and e-learning courses) to ensure that their employees have the know-ledge and skills they need in this area.
The courses on the schedule cover a wide range of subjects – from how to use different technologies correctly, to seminars focusing on safety-related qualifications – and are targeted at both operatives and managers. Offering basic and advanced theoretical and practical courses, BUCHEN and XERVON have, for example, trained more than 750 operatives to use respiratory protective equipment.
The SCC accreditation alone means that over 4,000 employees take part in health, safety and environmental protection seminars every year.
Health and safety have to be lived and experienced and be supported by everyone.
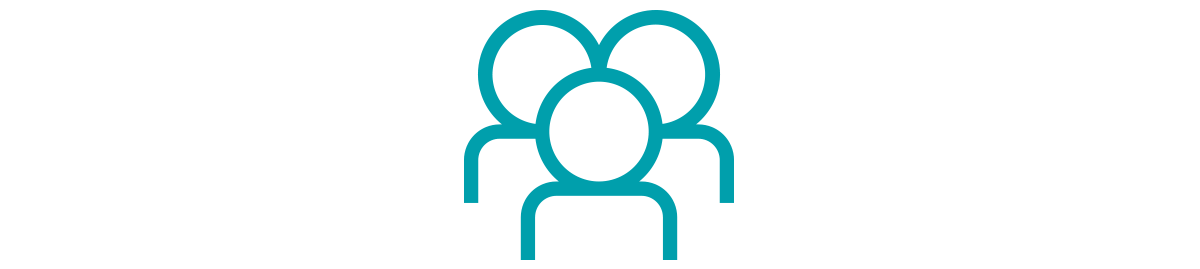
3. SaferTogether. An ambitious campaign.
Knowing what to do and actually doing it can be two quite different things when a person carries out their everyday tasks. The SaferTogether campaign was introduced around five years ago to prevent this from happening. Evaluated on a regular basis to check its effectiveness, this campaign primarily aims to raise awareness and make employees more mindful of health and safety at work. This multi-lingual safety campaign was initially put together for the operatives. Now, though, its focus has been widened to include managerial staff as well. The focal points have also changed over the years. While the centre of attention used to be on avoiding accidents, it is now looking at establishing common health and safety rules. Adrian Wortmann: “Health and safety have to be lived and experienced and be supported by everyone. By expanding the scope of our SaferTogether campaign, we are now also focusing on behavioural aspects so that our operatives and managers act proactively and out of conviction. Which means that managers are increasingly taking on a new role – that of being a supportive coach.”
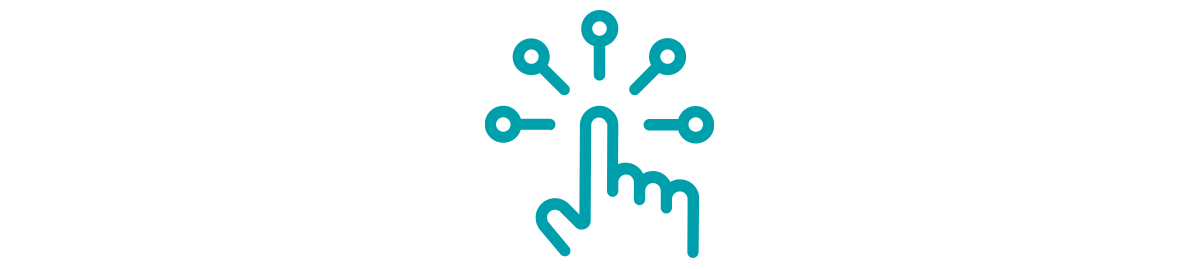
4. Packages of measures. Analogue & digital channels.
If employees are unable to access a computer at their workplace, then it is very difficult to contact them digitally. This means that hard copies are often the preferred method for providing QHSE information within the industrial services sector – and this is also true for the SaferTogether campaign. Just two examples: posters and flyers printed in up to 16 different languages and the credit card-sized LMRA cards. These cards enable operatives to carry out a last minute risk analysis just before they start their work. Before performing their first task, they systematically go through a list of questions to check that all the rules and regulations mentioned on the card have been met. If the answer to any of these questions is no, then they may not begin working. Thanks to this campaign, options are being looked at to create alternative digital solutions for workplaces that do not have a computer. These include setting up QR codes that operatives can then scan with their smartphones to access information on the internet. Relevant projects are currently being trialled. If they prove to be a success, then this would mean that the number of operatives who could be reached digitally would be more than doubled.
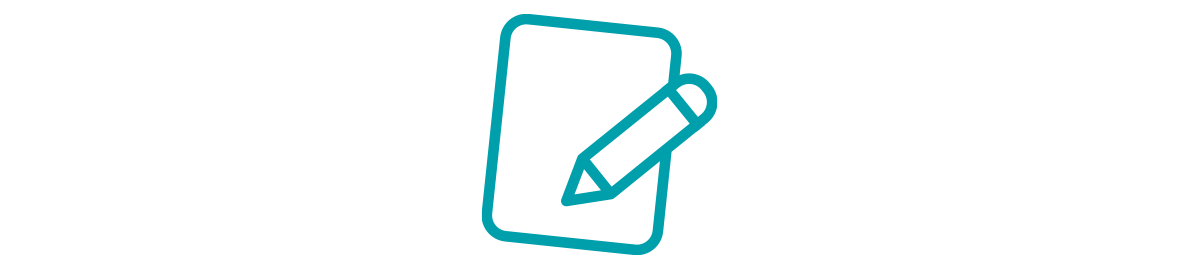
5. Preparation. Before work starts.
One thing is true for both BUCHEN and XERVON: the actual assignments that they are commissioned to do are not carried out at a moment’s notice. The first step they must do is to sit down and plan the work meticulously – a job that includes organising both the operational tasks as well as all safety-relevant aspects. The latter can require a long chain of preparatory steps before an assignment can actually be carried out, especially if high risk tasks have to be performed. Extensive investigations need to be completed to evaluate all conceivable risks, project-related risk assessments have to be compiled and a solution has to be drawn up that sets out all of the required safety measures right down to the smallest detail. A task that often results in this preparation work taking much longer to finish than the actual assignment itself.
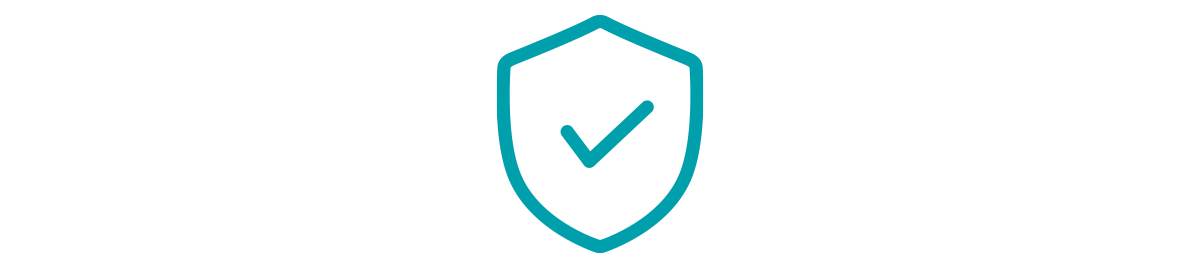
6. Protective gear. A safe companion.
No matter whether it involves personal protective equipment, respiratory protective gear or gas measuring instruments: both BUCHEN and XERVON’s core business requires their safety equipment to be working exactly as it should. Both industrial service companies run their own workshops so that their teams of operatives can rest assured that their safety systems are always in good working order. The service engineers at these workshops make sure that all safety equipment is fit for purpose. At the same time, both companies make the most of their practical experience to come up with innovations and improvements that can further augment safety at work. Such initiatives have seen them helping to create new standards, such as the DIN 19430 norm that covers protective clothing worn while carrying out high pressure water jetting tasks.
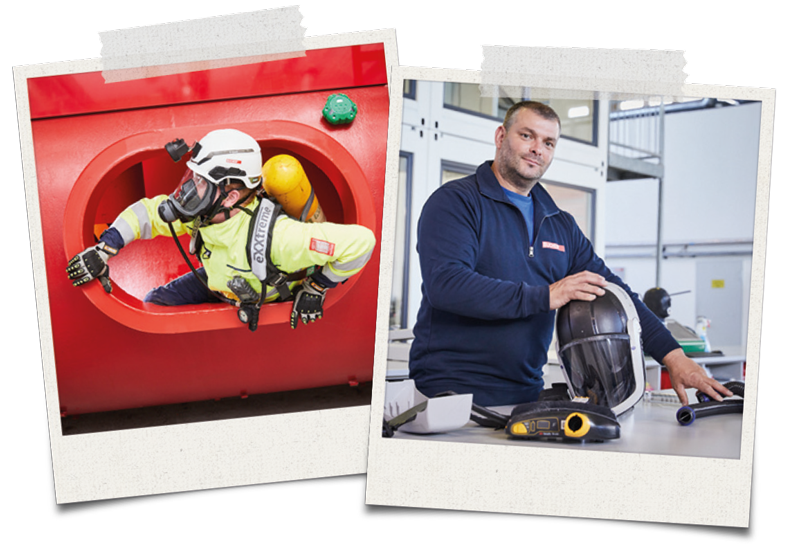
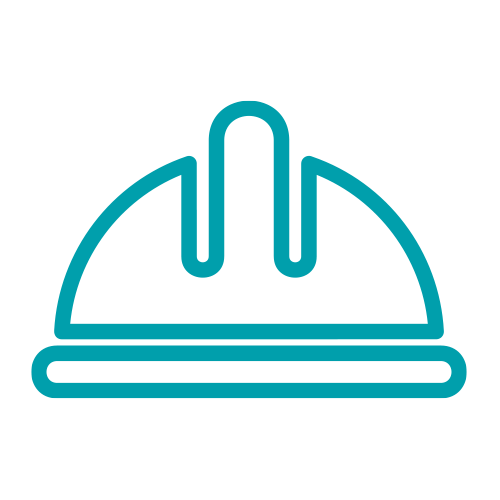
7. SafetyService. The name says it all.
Having worked in their industry for so many years, BUCHEN and XERVON have become true health and safety experts. And they both believe that it is only right to make their extensive safety know-how available to others as well. Which is why XERVON takes on QHSE tasks for its industrial clients by providing them, for example, with specialist officers. BUCHEN’s SafetyService division offers safety management support to companies, public institutions, fire brigades and the emergency services. Its portfolio of services focuses on safety-related equipment and how to use it and covers the whole range of gear – from full-body protection all the way through to more unusual types of safety equipment. Besides offering advisory, training and maintenance services, SafetyService also sells and rents out safety-related devices and products. By setting up Safety Shops and automatic dispensers (so-called Service Points), customers can access the safety equipment they need 24/7. SafetyService operates two centres of excellence in Leuna and Cologne. A third centre is due to be opened up in Bottrop in May.
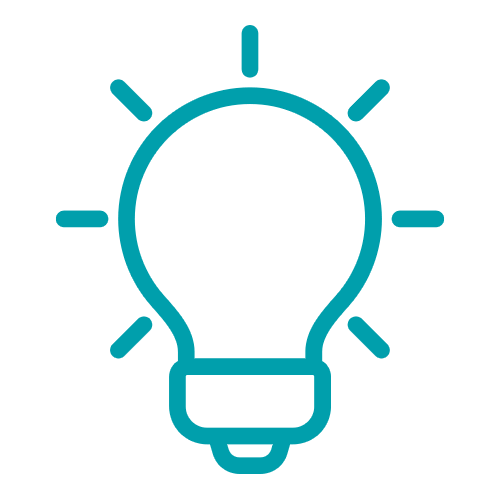
8. In-house developments. Innovations to grow safety.
BUCHEN and XERVON regularly work on innovations to further enhance the safety levels of the technology used in the industrial service sector. Focus here is put on both developing new technology and further developing existing systems so that the teams of operatives work under the very best conditions. One particularly promising route here is automating processes and procedures as this means that machines, systems and robots can carry out physically demanding and/or dangerous work on behalf of the operatives. Progress that is invaluable when it comes to health and safety: tasks that used to see the operatives having to don hazmat suits and climb into a customer’s facility can now be performed from a safe distance by using automated systems. BUCHEN’s list of in-house developments in this area is particularly long. It has, for example, developed an automated system to clean cement furnaces, a closed-loop system to clean heat exchangers and a robot that can perform high pressure water jetting work.
Over 600 measures aimed at improving processes were documented in 2022. More than 60 ideas and suggested improvements came from the employees.
If so many things have already been done and so many advances achieved, then maybe it is only logical to ask whether and how further progress can really be made. Isn’t the point eventually reached where it is simply not possible to make things safer? Adrian Wortmann commented: “Probably not. Working conditions and environments change, new technologies and findings open up new opportunities.
Improving health and safety at work is an ongoing process and it is vital to keep up to date at all times. As far as we’re concerned, enhancing, optimising and innovating equipment will continue to be at the very top of our list of priorities.”
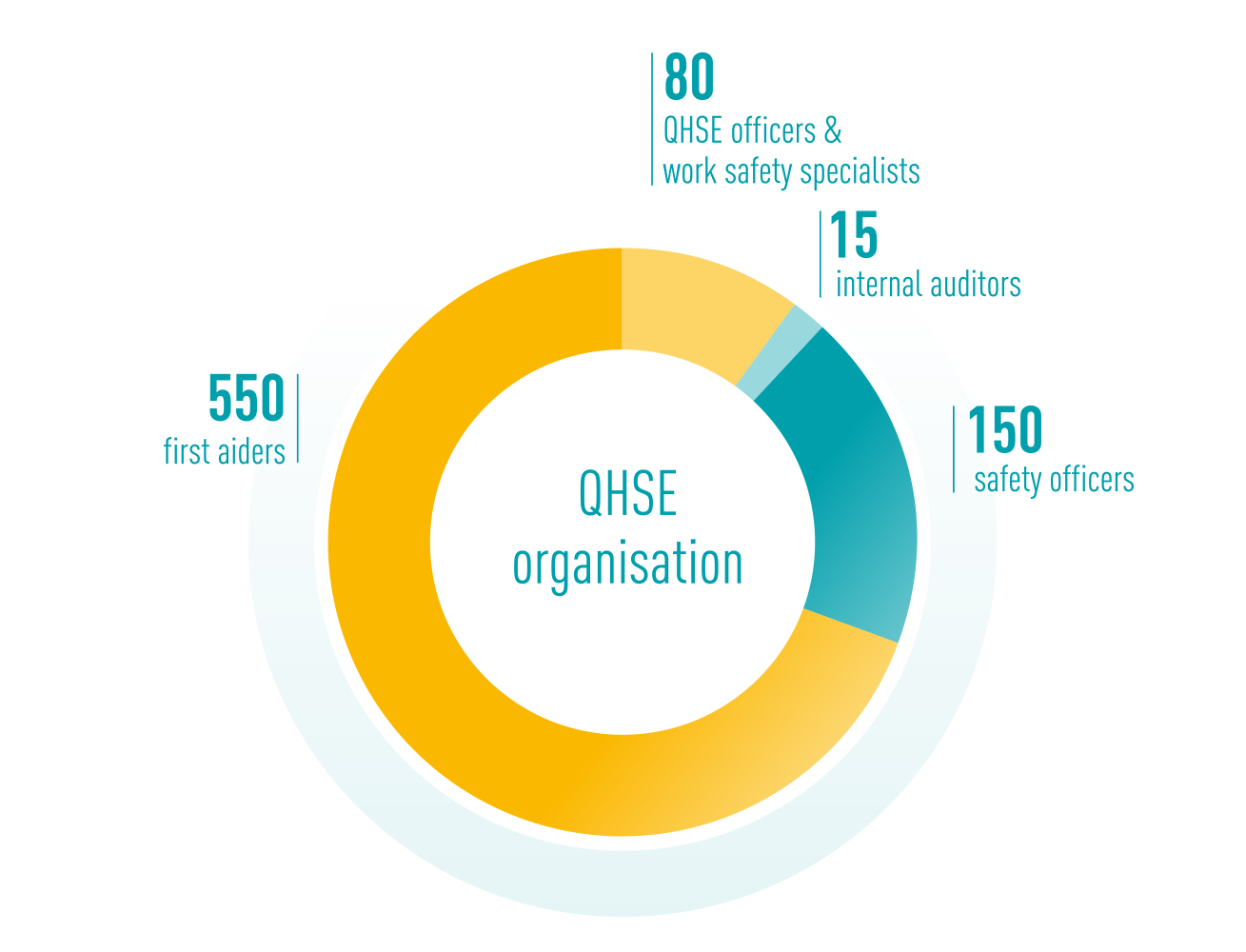
Image credits: image 1: Adobe Stock: svetazi, Adobe Stock: gradt; image 2, 3, 5, 6: © REMONDIS; image 4: Adobe Stock: BillionPhotos.com